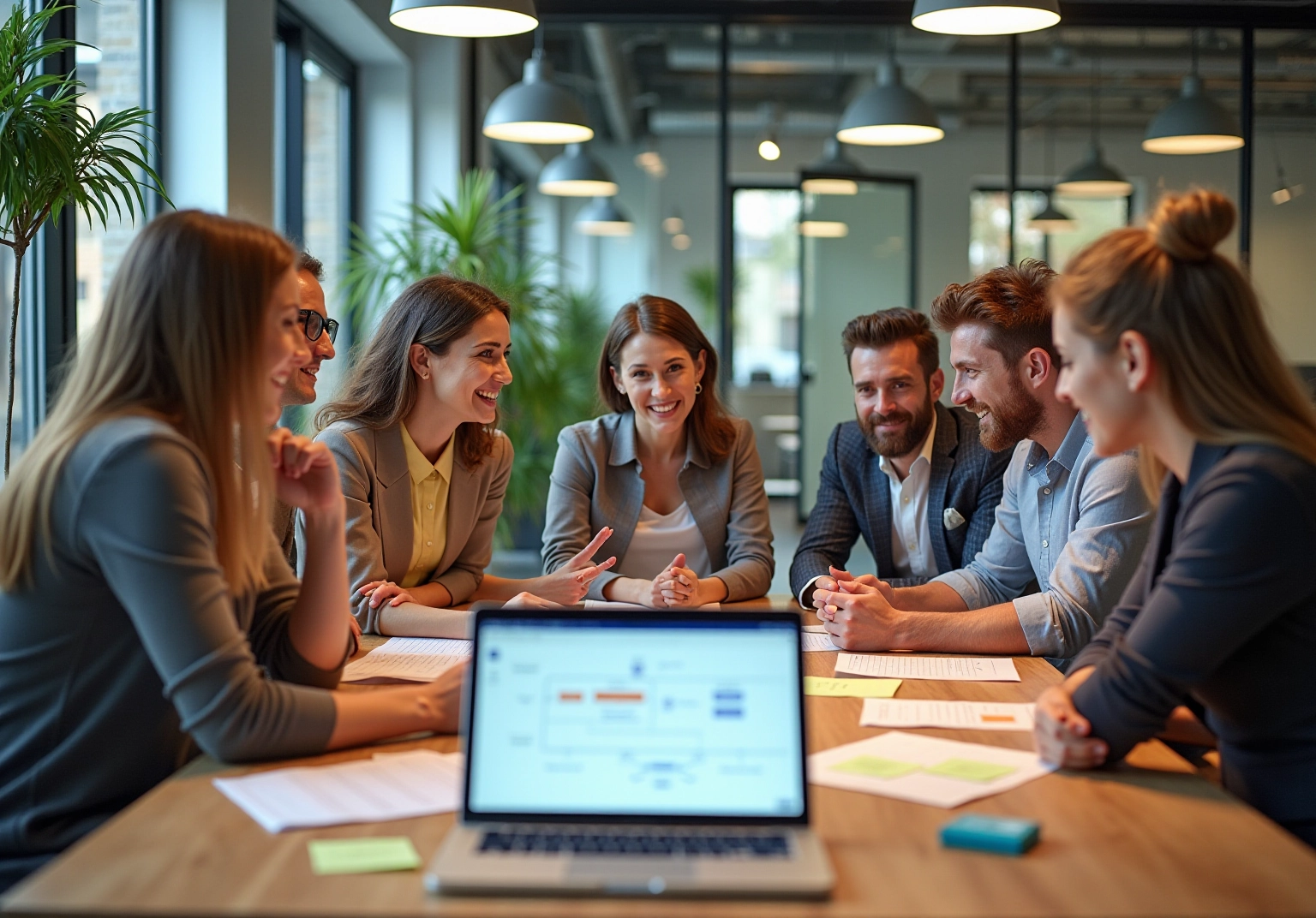
Knowledge Management through Documentation
|
August 14, 2025
|
10 Ideas to Improve Process Efficiency with Proven Strategies
Overview
You might be curious about how to boost process efficiency in your organization. Well, this article shares ten proven strategies that can help! From methodologies like Kaizen and Six Sigma to Business Process Automation, these approaches are all about streamlining operations and cutting down on waste. Each strategy comes with solid evidence showing how they can lead to significant productivity gains and cost reductions. So, let’s dive into how these methods can enhance your organizational performance!
Key Highlights:
- SowFlow helps streamline documentation, saving time and reducing inefficiencies in document workflows.
- Workers spend an average of 4.3 hours weekly searching for misplaced files, highlighting the need for better documentation tools.
- The Kaizen approach encourages incremental improvements, leading to productivity gains of 15-30% within the first year.
- Six Sigma focuses on reducing defects through data-driven decision-making, utilising the DMAIC framework for systematic process improvement.
- Business Process Automation (BPA) enhances efficiency by automating repetitive tasks, with 78% of leaders believing it boosts productivity.
- Lean methodologies aim to eliminate waste, achieving efficiency gains of 25-30% and improved customer satisfaction.
- Total Quality Management (TQM) fosters a culture of quality, resulting in productivity boosts of 15% and cost reductions of 20%.
- The Theory of Constraints (TOC) identifies bottlenecks, improving operational efficiency and resource utilisation.
- The 5 Whys technique uncovers root causes of problems, promoting effective collaboration and continuous improvement.
- Process improvement consultants provide tailored strategies that can lead to a 50% boost in productivity and significant ROI.
Introduction
In today’s competitive business world, you might be wondering just how crucial process efficiency really is. Organizations are always on the lookout for fresh strategies that not only make operations smoother but also boost productivity and cut down on waste. This article dives into ten tried-and-true methods that can really amp up your process efficiency, packed with insights and practical steps you can take. But with so many options out there, how do businesses figure out which strategies will actually deliver the goods? Let’s explore these techniques together and uncover the answers, helping you elevate your operational effectiveness and stay ahead of the game.
SowFlow: Streamline Documentation for Enhanced Process Efficiency
You might be wondering how to make your business documentation a breeze. Well, let me introduce you to SowFlow—it's a powerful tool that helps companies create and manage their documentation effortlessly. With advanced technology at your fingertips, you can whip up comprehensive how-to guides in no time! This means your team can access essential information right when they need it, cutting out those pesky delays.
Now, think about it: how much time do you waste searching for documents? Studies show that the average worker spends about 4.3 hours a week just looking for misplaced files. Plus, over 55% of businesses struggle with inefficient document workflows, emphasizing the importance of ideas to improve process in order to reduce wasted resources and lost productivity. That's where SowFlow shines! It not only saves you time but also provides ideas to improve process in knowledge management by tackling common issues like creating, finding, and updating information.
And here's something cool: with SowFlow's user-friendly Chrome extension, your team can document workflows straight from their browser. This makes recording tasks quick and easy! As Mark Fairlie puts it, "Forty-eight percent of employees say it's hard to find documents quickly." So, why not take a step towards exploring ideas to improve process for better operational effectiveness? By incorporating SowFlow's solutions, you can boost performance and compliance across the board. Let's dive into how this can transform your documentation process!
Kaizen Method: Foster Continuous Improvement in Processes
You might be wondering how the Kaizen approach can really make a difference in your workplace. Well, it’s all about those ongoing, incremental advancements in processes that encourage everyone on the team to share their ideas to improve process workflows. This inclusive method doesn’t just boost morale; it leads to significant productivity gains as those little tweaks add up over time. Regular Kaizen events are key to identifying inefficiencies and developing ideas to improve processes that drive better performance and productivity.
Now, here’s something interesting: organizations that embrace Kaizen practices often see productivity improvements of 15-30% within the first year! And guess what? This figure can climb even higher when you use tools like SowFlow. Take Siemens AG and Danaher Corporation, for example; they’ve successfully implemented the five-step Kaizen method and have seen impressive enhancements in both efficiency and productivity.
Speaking of tools, let’s talk about the Kaizen Wheel framework. It includes six philosophies for ongoing development, helping companies create a structured environment that encourages continuous improvements. Anastasia Masadi, a Product Owner, really captures this synergy when she says, "SowFlow has been a game changer in the way we document work and deliver to our clients. I do not have to take each screenshot separately, and do not even have to leave the browser while I am creating SOPs and training materials. SowFlow gave me time from my life back." This demonstrates how integrating efficient documentation solutions like SowFlow can generate ideas to improve processes, complementing Kaizen practices and driving even more productivity and workflow enhancements. So, what are you waiting for? Let’s dive into how you can make these changes work for you!
Six Sigma: Minimize Defects and Enhance Quality Control
You might be wondering, what exactly is Six Sigma? Well, it's a super effective methodology focused on cutting down defects and boosting quality control in systems. By using statistical analysis and making decisions based on data, organizations can develop ideas to improve process, spot variations, and take corrective actions that really enhance performance outcomes.
Now, let's talk about the DMAIC framework—this stands for Define, Measure, Analyze, Improve, Control. Ideas to improve process are at the heart of Six Sigma and assist teams in tackling problems systematically. When companies embrace Six Sigma principles, they can develop ideas to improve process, achieve top-notch quality outputs, reduce waste, and ultimately ramp up their operational performance. Sounds pretty great, right?
Business Process Automation: Automate Tasks to Boost Efficiency
You might be wondering how business activity automation (BPA) can really make a difference in your organization. Well, it’s all about using technology to take care of those repetitive tasks and streamline your workflows. This means you can significantly boost your efficiency! By embracing BPA, companies like yours can cut down on the time spent on manual processes, lessen errors, and ramp up productivity. Tools like those from SowFlow can handle everything from data entry to report generation and customer communications, freeing up your team to focus on more valuable work.
Now, let’s talk about what happens when organizations start using BPA. They often see faster turnaround times and better accuracy, which leads to a noticeable boost in productivity. SowFlow not only offers unlimited access to all its software features but also provides dedicated customer success support and training in best practices. This combo really helps enhance your documentation strategies.
Did you know that:
- 78% of business leaders believe automation boosts productivity?
- 90% of IT pros report seeing business growth thanks to process automation?
- 51% of business leaders say automation can cut overall costs by 10 to 50%?
Just look at firms like Shell—they’ve successfully woven automation into their processes, achieving impressive cost savings and productivity gains. For instance, a major insurance company slashed its claims processing time by 70% through automation. That’s how BPA can transform your operational efficiency!
But wait, there’s more! Automation doesn’t just make tasks easier; it’s also reshaping workflows for the future. By 2025, it’s expected that 70% of employees will be using AI to automate or enhance their work tasks. This shift towards intelligent automation enables businesses to focus on strategic initiatives and develop ideas to improve processes instead of getting bogged down by repetitive tasks. And here’s a fun fact: about 30% of business leaders report lower labor costs thanks to process automation.
In conclusion, incorporating BPA into your business isn’t just a passing trend; it’s a strategic move for those looking to enhance productivity and operational effectiveness in today’s competitive landscape. If you’re curious about how to get started, why not test out automation tools like SowFlow in one department first? This way, you can see the productivity improvements before rolling it out company-wide. For more details on pricing and to discover how SowFlow can support your organization, feel free to reach out!
Lean Process Improvement: Eliminate Waste for Greater Efficiency
You might be wondering how Lean improvement can really make a difference in your organization. Well, it’s all about systematically cutting out waste to boost operational efficiency. By spotting those non-value-added tasks and fine-tuning workflows, businesses can generate ideas to improve process and enhance their operations, delivering more value to their customers. Continuous assessment is a hallmark of Lean methodologies, which encourages teams to generate ideas to improve process and effectively measure the outcomes.
Now, let’s dive into some techniques! Tools like value stream mapping and the 5S methodology are super helpful in visualizing processes and generating ideas to improve process in areas that need a little TLC. Companies that have jumped on the Lean bandwagon often report an efficiency gain of 25-30%. That’s not just a number; it translates to lower costs and a big boost in productivity!
And here’s something to think about: organizations using Lean strategies are 90% more likely to hit or surpass customer satisfaction goals. Plus, 85% of companies that embrace these strategies see improved customer satisfaction scores. This really underscores how effective these methodologies are in driving operational excellence. As we look ahead to 2025, the implementation of Lean principles is evolving, with companies focusing more on data-driven decisions and generating ideas to improve process by getting employees involved to foster a culture of continuous improvement.
Total Quality Management: Cultivate a Culture of Quality for Efficiency
Total Quality Management (TQM) is all about creating a culture of continuous improvement and quality in every corner of an organization. You might be wondering how that works. Well, TQM empowers employees at all levels to take ownership of their work and get actively involved in making things better. This holistic approach not only boosts the quality of products and services but also generates ideas to improve process as companies refine their operations. The core principles of TQM focus on:
- Keeping the customer happy
- Involving employees
- Managing processes carefully
These are key ingredients for building a more effective and efficient organization.
Now, let’s talk numbers! In 2025, organizations that embraced TQM saw some impressive gains in operational efficiency and quality. For example, companies implementing TQM strategies reported:
- An average productivity boost of 15%
- A cost reduction of 20%
Take AtlantiCare, a healthcare provider, for instance. Through TQM initiatives, they managed to triple their repeat customer numbers and skyrocket their revenues from $280 million to $650 million. Pretty amazing, right?
But there’s more to TQM than just numbers. It cultivates a quality-driven culture by promoting regular feedback and encouraging employees to contribute their ideas to improve process in quality improvement efforts. This collaborative approach not only lifts morale but also leads to smarter decision-making and sparks innovation. As businesses tackle the challenges of today's market, implementing ideas to improve process through TQM principles becomes crucial for staying competitive and meeting those ever-growing customer expectations.
In summary, the impact of TQM on operational efficiency and quality is significant. Organizations that adopt it often find themselves with streamlined operations and happier customers. By embracing TQM, businesses can nurture a culture of quality that fuels continuous improvement and operational excellence. So, why not dive deeper into TQM and see how it can transform your organization?
Theory of Constraints: Identify and Address Bottlenecks
You might be wondering about the Theory of Constraints (TOC) and why it’s such a big deal in management. Well, TOC is all about spotting and tackling the biggest limiting factor in any system. By focusing on those pesky bottlenecks, organizations can really boost their workflows and overall efficiency. It encourages a systematic look at processes to identify constraints, leading to ideas to improve process that allow teams to whip up targeted solutions to ease those bottlenecks. This isn’t just about cranking up throughput; it’s also about making better use of resources and ramping up productivity across the board.
Now, let’s talk about what’s happening with TOC these days. It’s becoming more relevant in all sorts of industries, especially as companies try to keep up with fast-paced market changes. Many are pairing Lean Manufacturing techniques with TOC principles to really streamline their operations. You might hear about methods like Kanban and Total Productive Maintenance (TPM) being used to sync production activities with constraints, which helps improve the overall system throughput.
Real-life stories show just how effective TOC can be in tackling bottlenecks. Organizations that have jumped on the TOC bandwagon often report big boosts in operational efficiency. For example, Gwangjae Yu pointed out that a recent study found a 35% drop in average work-in-process (WIP) levels in semiconductor manufacturing by using optimization techniques that align with TOC principles. This drop not only ramped up production capacity but also cut down on operational costs, highlighting the double whammy benefits of TOC.
As we move into 2025, more and more entities are realizing how important it is to keep an eye on their bottleneck analysis methods and explore ideas to improve process. Sarah Lee emphasizes that bottleneck analysis isn’t just a one-and-done task; it’s a continuous journey that needs regular monitoring and enhancement. By tapping into data-driven decision-making and fostering cross-functional collaboration, businesses can generate ideas to improve process, effectively spot and resolve constraints, and pave the way for ongoing operational excellence. Keeping TOC principles in play is essential for any entity looking to boost productivity and maintain a competitive edge in today’s ever-changing business landscape.
DMAIC Framework: Systematic Approach to Process Improvement
You might be wondering how the DMAIC framework—Define, Measure, Analyze, Improve, and Control—can really make a difference in enhancing processes within the Six Sigma methodology. Well, this structured method is like a trusty toolkit that helps organizations systematically generate ideas to improve processes by spotting inefficiencies, digging into root causes, and rolling out effective solutions. By following the DMAIC steps, teams ensure their improvements are not just data-driven but also sustainable, leading to better efficiency and operational effectiveness.
Fast forward to 2025, and you'll find that many organizations have jumped on the DMAIC bandwagon to streamline their operations. Take, for example, a nonprofit organization that used DMAIC to boost its fundraising conversion rates from 45% to 52%. How did they do it? By fine-tuning their outbound call strategies! They set success metrics, evaluated call effectiveness using specific KPIs, analyzed data for insights on call timing and script usage, and made targeted enhancements based on their findings.
The impact of DMAIC on operational performance is pretty impressive. Organizations that embrace this methodology often report significant boosts in productivity and quality. For instance, companies that weave data-driven decision-making into the DMAIC framework can see a 15-25% drop in operational expenses and a 30-40% uptick in resource utilization. These results really highlight how important ideas to improve processes are for driving efficiency.
Experts in the field emphasize just how crucial the DMAIC methodology is. It provides a clear roadmap for tackling challenges based on solid facts rather than assumptions, which means companies can make informed decisions. As Bill Smith, the brain behind the Six Sigma Training program, puts it, "Six Sigma’s aim is to enhance overall workflows to that standard of quality or higher." This organized approach not only ramps up operational effectiveness but also gears companies up for ongoing success in a competitive landscape.
5 Whys: Uncover Root Causes to Drive Efficiency
You might be wondering, what exactly is the 5 Whys technique? Well, it’s a straightforward yet powerful problem-solving method that helps teams dig deep into issues by persistently asking 'Why?' until they uncover the core problem. This approach encourages teams to look beyond surface-level symptoms and really explore the underlying causes. By systematically applying the 5 Whys, organizations can uncover ideas to improve process and implement focused improvements that significantly enhance overall efficiency.
For example, companies like Toyota have successfully used the 5 Whys to streamline their operations and boost reliability. This technique not only fosters a culture of inquiry but also enables teams to collaborate effectively, sharing insights that lead to stronger solutions. Looking ahead to 2025, more organizations are integrating the 5 Whys with digital tools to enhance their root cause analysis capabilities, ensuring they can keep pace with the rapid changes in the business landscape.
So, how can you apply the 5 Whys effectively? Start with a specific problem and document each answer as you ask 'Why?' This iterative method clarifies the connections between various root causes and helps teams align on final conclusions. Plus, utilizing SowFlow's instant documentation solution can really streamline this process, allowing teams to create user guides effortlessly and keep their findings up to date in real-time. For instance, with SowFlow, teams can quickly document each step of their 5 Whys analysis, ensuring that valuable insights are captured and easily accessible for future reference. As Linsa Saji puts it, "By asking 'why' five times, project managers can delve into the underlying causes of problems." By focusing on root causes, organizations can implement ideas to improve process that not only address current issues but also prevent similar challenges from arising in the future.
And don’t forget, setting benchmarks to assess the effectiveness of the solutions derived from the 5 Whys analysis is crucial for ongoing development and accountability. Why not start using SowFlow today to enhance your 5 Whys process and boost productivity in your company?
Process Improvement Consultants: Leverage Expertise for Efficiency Gains
You might be wondering how process enhancement advisors can really help your company boost productivity. Well, these experts dive deep into your current workflows to spot inefficiencies and offer ideas to improve process with tailored strategies for optimization.
By teaming up with these consultants, you can adopt best practices and proven methodologies that often lead to impressive efficiency gains. For example, companies using business process management (BPM) tools typically see a 50% boost in productivity and a whopping 90% cut in cycle time.
Plus, did you know that 80% of organizations with BPM initiatives report an internal ROI greater than 15%? This trend really highlights how tapping into external expertise can provide ideas to improve process and transform your operational performance.
As we head into the complexities of 2025, bringing in consultants will be key to driving efficiency and hitting those strategic goals.
Conclusion
You might be wondering how to make your organization thrive in today’s competitive landscape. Well, implementing effective strategies for process efficiency is key! This article has looked at some proven methods that can really make a difference, like innovative tools such as SowFlow, the Kaizen approach, Six Sigma, business process automation, Lean methodologies, Total Quality Management, the Theory of Constraints, the DMAIC framework, the 5 Whys technique, and the role of process improvement consultants. Each of these strategies brings unique insights and actionable steps that can significantly boost your operational effectiveness.
Let’s break it down a bit. Continuous improvement and data-driven decision-making are super important. For example, SowFlow helps streamline documentation, while the Kaizen method encourages a culture of ongoing enhancements. Six Sigma and the DMAIC framework offer structured ways to minimize defects and improve quality, and Lean methodologies are all about cutting out waste. Plus, embracing automation can lead to some impressive productivity gains, and getting help from process improvement consultants can really speed up your efficiency.
So, what’s the takeaway? Enhancing process efficiency isn’t just a nice-to-have; it’s a must for sustainable growth. By exploring these strategies and weaving them into your daily operations, you can not only improve workflows but also nurture a culture of innovation and responsiveness. As the landscape keeps evolving, taking proactive steps toward process improvement will be essential for staying ahead of the curve and meeting future demands. Now, doesn’t that sound like a plan?
Frequently Asked Questions
What is SowFlow and how does it help with documentation?
SowFlow is a powerful tool designed to help companies create and manage their documentation effortlessly. It enables teams to quickly produce comprehensive how-to guides, ensuring essential information is accessible when needed, which reduces delays in workflows.
How much time do employees typically spend searching for documents?
Studies indicate that the average worker spends about 4.3 hours a week searching for misplaced files.
What are some common issues that SowFlow addresses?
SowFlow tackles common documentation issues such as creating, finding, and updating information, thereby improving knowledge management and process efficiency.
How does SowFlow's Chrome extension benefit users?
SowFlow's user-friendly Chrome extension allows teams to document workflows directly from their browser, making it quick and easy to record tasks.
What is the Kaizen method and how does it improve workplace processes?
The Kaizen method focuses on ongoing, incremental improvements in processes by encouraging team members to share ideas. This inclusive approach boosts morale and can lead to significant productivity gains.
What productivity improvements can organizations expect from implementing Kaizen practices?
Organizations that adopt Kaizen practices often see productivity improvements of 15-30% within the first year.
How does SowFlow complement the Kaizen method?
SowFlow enhances the Kaizen method by providing efficient documentation solutions that help identify inefficiencies and generate ideas for process improvements, driving productivity and workflow enhancements.
What is Six Sigma and its primary focus?
Six Sigma is a methodology aimed at reducing defects and enhancing quality control in systems through statistical analysis and data-driven decision-making.
What does the DMAIC framework in Six Sigma stand for?
DMAIC stands for Define, Measure, Analyze, Improve, and Control, and it is a structured approach used to tackle problems systematically within the Six Sigma methodology.
How does Six Sigma contribute to process improvement?
By embracing Six Sigma principles, organizations can identify variations, take corrective actions, and ultimately improve quality outputs, reduce waste, and enhance operational performance.
👍
What others are liking
5 Steps to outline your ideal documentation structure
5 MINS READ
Where to start the your journey of mapping out your ideal documentation structure, aligning it with the very heartbeat of your organization?
Defining a winning level of detail in your process
3 MINS READ
What is too much detail, and what is too little? This article described in that winning level detail about what detail is enough.