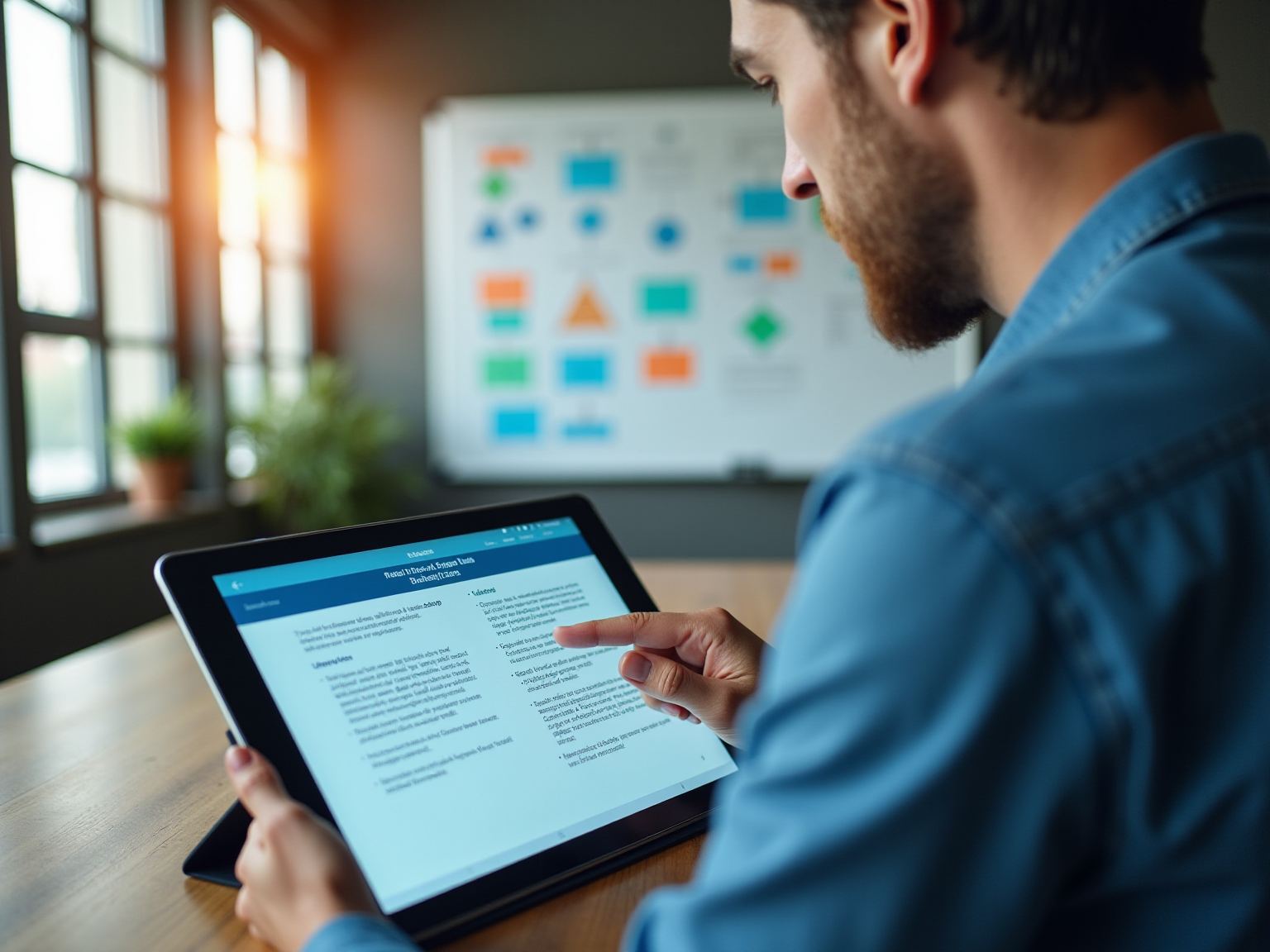
Process Improvement through Documentation
|
July 15, 2025
|
Work Instruction vs Standard Operating Procedure: Key Differences Explained
Overview
You might be wondering what sets Work Instructions apart from Standard Operating Procedures (SOPs). Well, the key differences really come down to their scope and detail. Work Instructions zoom in on specific tasks, offering step-by-step guidance, while SOPs take a broader view, outlining entire processes along with roles and responsibilities. It’s like having a detailed map for a single route versus a general overview of an entire journey.
Now, let’s dive into why this distinction matters. Work Instructions boost operational efficiency by guiding you through each task in detail, making sure nothing gets overlooked. On the flip side, SOPs are all about ensuring compliance and standardization across workflows. Together, they play complementary roles in effective documentation practices, helping you navigate the complexities of your work with ease. So, how do you use these tools to your advantage? That’s where the fun begins!
Key Highlights:
- Work Instructions are detailed, step-by-step guides that focus on specific tasks, enhancing operational efficiency.
- Standard Operating Procedures (SOPs) provide a broader framework for processes, outlining roles, responsibilities, and overall objectives.
- Both Work Instructions and SOPs improve operational efficiency, facilitate onboarding, and standardize practices across teams.
- Case studies show that digital formats for guidelines, such as augmented reality, can significantly enhance employee efficiency.
- Work Instructions are flexible and can be quickly updated, making them essential for fast-paced environments.
- SOPs ensure compliance with regulations and provide structured frameworks for critical tasks, such as emergency response.
- Investing in solid documentation practices can lead to improved productivity and reduced operational challenges.
- Tools like SowFlow and ClickUp's SOP Template streamline the creation and maintenance of documentation, reflecting modern operational needs.
Introduction
In the intricate landscape of organizational operations, you might be wondering about the roles of Work Instructions and Standard Operating Procedures (SOPs). These two elements are pivotal for achieving efficiency and compliance. While Work Instructions provide the nitty-gritty, step-by-step guidance essential for executing specific tasks, SOPs offer a broader framework that outlines the overall processes and policies governing an organization. This distinction is critical! Both are designed to enhance operational consistency, streamline training, and foster a culture of continuous improvement.
Now, as businesses increasingly recognize the value of effective documentation, understanding how these two tools interact becomes vital for navigating the complexities of modern industry. By delving into their definitions, differences, benefits, and real-world applications, organizations can unlock the full potential of Work Instructions and SOPs. This exploration can drive success in an ever-evolving landscape. So, let’s dive in and explore how you can make the most of these essential tools!
Define Work Instructions and Standard Operating Procedures
You might be wondering what Work Instructions are all about. Well, they’re detailed, step-by-step guides that show you how to tackle specific tasks within a process. They really focus on the 'how' of getting things done, providing those granular details that are essential for you to perform your duties accurately. By checking out the time it takes to complete the steps in these instructions, organizations can spot potential bottlenecks and areas for improvement, which is a great way to boost operational efficiency.
Now, let’s talk about Standard Operating Procedures (SOPs). These are broader documents that lay out the overall processes and policies that guide operations. SOPs provide a comprehensive framework for task execution, detailing objectives, responsibilities, and the sequence of actions needed to achieve specific outcomes. While operational guidelines zoom in on task-specific directions, SOPs cover a wider range, clarifying the reasoning and context behind the processes.
The importance of both task guidelines and SOPs in business documentation can’t be overstated. They not only ramp up efficiency in operations but also make onboarding smoother and help standardize practices across teams. For example, consider a case study on using augmented reality in job guidelines. It shows how frontline employees, who often rely on outdated paper guidelines, can significantly boost their efficiency by transitioning to digital formats. This switch not only streamlines task execution but also aligns with modern operational practices, highlighting the broader implications for organizations.
As a reminder, "Once you’ve made any necessary revisions, your task guideline should be ready for use!" This little nugget underscores the practical readiness of task guidelines, emphasizing their role in effective documentation. Plus, incorporating Lean Six Sigma tools and techniques can further enhance business success, reinforcing the value of solid documentation practices.
In summary, while work instruction vs standard operating procedure each have their own roles, blending them together is key for effective documentation and operational success within organizations. So, what’s your take on these practices? Are there areas in your organization where you think they could make a difference?
Contrast Key Differences Between Work Instructions and SOPs
You might be wondering about the main differences in the context of work instruction vs standard operating procedure (SOPs). Well, they’re pretty distinct when it comes to their scope, detail, and purpose. Work guidelines are all about the nitty-gritty; they focus on specific tasks and provide step-by-step guidance for getting things done. Just think about it—'Work guidelines provide comprehensive, step-by-step directions,' which is super important for keeping everything running smoothly. For instance, a guideline might go into detail about how to operate a specific machine, covering essential safety measures and troubleshooting tips.
Now, on the flip side, SOPs take a broader view. They encompass entire workflows and outline the roles and responsibilities of different team members. Imagine an SOP as a big-picture overview of the production process, detailing everything from acquiring raw materials to delivering the final product, but without diving into every tiny task.
While task guidelines are mainly for training and ensuring everyone’s on the same page, SOPs act as compliance documents that uphold organizational standards. The cool thing about task guidelines is their flexibility—they can be updated quickly, making them perfect for adapting to changing operational needs. This is especially crucial in fast-paced environments where processes can shift frequently.
Moreover, task guidelines are essential for knowledge sharing across the organization, helping to keep employee expertise sharp and ensuring vital information is always accessible. For example, a case study on standard operating procedures in emergency response really highlights their importance. They provide a structured framework for action during crises, ensuring the safety and security of both staff and customers. As industries increasingly recognize the value of integrating work instruction vs standard operating procedure, there’s a noticeable trend towards improving operational efficiency and compliance. Tools like ClickUp's SOP Template are making it easier than ever to create and maintain standardized procedures, reflecting the modern shift towards more efficient documentation practices. So, how are you handling your documentation challenges?
Explore Benefits of Work Instructions and SOPs
Explore the Benefits of Work Instructions and SOPs
You might be wondering why work instructions are so important. Well, they offer a bunch of advantages! For starters, they boost task accuracy, cut down training time, and help employees feel more confident. By laying out clear, detailed steps, the comparison of work instruction vs standard operating procedure really helps reduce the risk of errors, ensuring that tasks are done consistently. This is super important in places like manufacturing and healthcare, where even a tiny mistake can lead to big problems. Sure, developing, managing, and sharing operational guidelines can be a bit pricey in terms of time and money, but trust me, it’s worth it. Companies that skip out on solid task guidelines often find themselves facing all sorts of issues, like lower efficiency and increased safety risks, which can really put a dent in their success. There’s even a case study that shows manufacturing firms that ignore detailed task instructions end up struggling with operational challenges, leading to lower productivity and a higher chance of accidents.
Now, let’s talk about work instruction vs standard operating procedure (SOPs). They create a solid framework for compliance and standardization across the board. The distinction between work instruction vs standard operating procedure ensures that everyone knows the procedures and regulations that guide their work, which is key for maintaining quality and safety standards. Plus, they make onboarding new employees a breeze by giving them a comprehensive overview of how things work, effectively shortening that pesky learning curve. As Oxmaint puts it, 'SOPs simplify the audit process by providing well-organized documentation of compliance efforts.'
Speaking of efficiency, have you heard about SowFlow? It’s been a game changer for teams when it comes to recording tasks and delivering to clients. Anastasia Masadi, a Product Owner, shares, "I do not need to capture each screenshot individually, and do not even have to exit the browser while I am developing standard operating procedures and training materials. SowFlow gave me time from my life back." This kind of transformative effect on documentation efficiency allows organizations to whip up work instruction vs standard operating procedure and guidelines in no time, boosting productivity and enhancing user experience.
Both work instruction vs standard operating procedure are essential for enhancing knowledge management. They set up a centralized repository of information that’s easy to access and update. Investing in a solid SOP program is a no-brainer for strengthening regulatory compliance efforts, as it simplifies the audit process with well-organized documentation of compliance activities. By using these tools, organizations can foster a culture of ongoing improvement and excellence, ensuring that they fully reap the benefits of guidelines and SOPs.
Identify Use Cases for Work Instructions and SOPs
You might be wondering just how important work instruction vs standard operating procedure are, particularly in environments where precision and consistency are essential—consider manufacturing, healthcare, and technical support. Take a manufacturing facility, for instance; guidance is what helps operators assemble parts correctly, ensuring quality and operational efficiency. A notable example is Yura's 'CADvizor WORK', launched in January 2023. This tool assists factory workers in crafting electrical products by providing them with accurate product details and better techniques, showcasing how software can evolve to enhance productivity.
Now, let’s talk about SowFlow. It’s a game changer for teams looking to create user guides effortlessly. With SowFlow, you can make instant updates and revisions, keeping those work instructions fresh and relevant in our fast-paced business world. No more endless meetings trying to find answers! With just a single command, you can access vital documentation, making it super easy to get the info you need right when you need it.
On the flip side, let’s not forget about standard operating protocols, especially in industries like pharmaceuticals, food production, and aviation, where sticking to compliance standards is crucial. An SOP could lay out how to conduct safety inspections or quality checks, ensuring everyone is on the same page with legal and organizational requirements. As Quentin Creusot wisely points out, "Standard Operating Procedures are critical for maintaining compliance with regulatory standards," which really underscores their importance in organized documentation. Plus, there’s data showing that companies can save over $700K in waste marketing expenses by adopting efficient documentation practices, which really strengthens the argument for their role in operational excellence.
So, both operational guidelines and work instruction vs standard operating procedure are vital for training programs. Operational guidelines serve as handy resources, while standard procedures give a comprehensive view of how things work in an organization. With SowFlow, documentation takes a leap forward, allowing for easy user guide creation and quick updates, all of which boosts productivity and ensures that the differences between work instruction vs standard operating procedure are effectively understood and utilized in today’s operational landscape.
Conclusion
You might be wondering why understanding the distinct yet complementary roles of Work Instructions and Standard Operating Procedures (SOPs) is so crucial for organizations aiming for operational excellence. Well, Work Instructions are your go-to for detailed guidance on executing specific tasks. They ensure accuracy and consistency in performance, which is especially important in precision-driven environments—after all, even minor errors can lead to significant consequences. On the flip side, SOPs create a broader framework that outlines the processes and policies necessary for compliance and standardization across the organization. Their comprehensive nature helps employees navigate complex workflows effectively.
Now, let’s dive into how integrating these two documentation tools can really boost your training and knowledge management while fostering a culture of continuous improvement. Organizations that utilize both Work Instructions and SOPs can cut down training time, boost employee confidence, and streamline operational efficiency. As industries evolve, being able to adapt and update these documents quickly becomes a vital asset, helping organizations stay agile and responsive to changing demands.
Ultimately, using Work Instructions and SOPs strategically can lead to some fantastic benefits—from improved compliance and quality assurance to increased productivity and safety. By focusing on effective documentation practices, businesses can unlock their full potential, ensuring they’re ready to tackle the challenges of an ever-evolving landscape. Embracing these essential tools isn’t just a best practice; it’s a fundamental step toward sustained success and operational excellence. So, why not take that step today?
Frequently Asked Questions
What are Work Instructions?
Work Instructions are detailed, step-by-step guides that provide granular details on how to perform specific tasks within a process, focusing on the 'how' of getting things done.
How do Work Instructions help organizations?
By analyzing the time it takes to complete the steps outlined in Work Instructions, organizations can identify potential bottlenecks and areas for improvement, thereby boosting operational efficiency.
What are Standard Operating Procedures (SOPs)?
SOPs are broader documents that outline overall processes and policies guiding operations. They provide a comprehensive framework for task execution, detailing objectives, responsibilities, and the sequence of actions needed to achieve specific outcomes.
How do Work Instructions and SOPs differ?
While Work Instructions focus on task-specific directions and the detailed 'how', SOPs cover a wider range, clarifying the reasoning and context behind processes.
Why are Work Instructions and SOPs important in business documentation?
They enhance operational efficiency, facilitate smoother onboarding, and help standardize practices across teams.
Can you provide an example of how modern technology can improve task guidelines?
A case study on using augmented reality in job guidelines shows that frontline employees can significantly boost their efficiency by transitioning from outdated paper guidelines to digital formats.
What should be done after revising a task guideline?
Once necessary revisions have been made, the task guideline should be ready for use, emphasizing its practical readiness in effective documentation.
How can Lean Six Sigma tools enhance business success?
Incorporating Lean Six Sigma tools and techniques can further improve business success by reinforcing the value of solid documentation practices.
What is the key takeaway regarding Work Instructions and SOPs?
The effective blending of Work Instructions and SOPs is crucial for successful documentation and operational success within organizations.
👍
What others are liking
5 Steps to outline your ideal documentation structure
5 MINS READ
Where to start the your journey of mapping out your ideal documentation structure, aligning it with the very heartbeat of your organization?
Defining a winning level of detail in your process
3 MINS READ
What is too much detail, and what is too little? This article described in that winning level detail about what detail is enough.