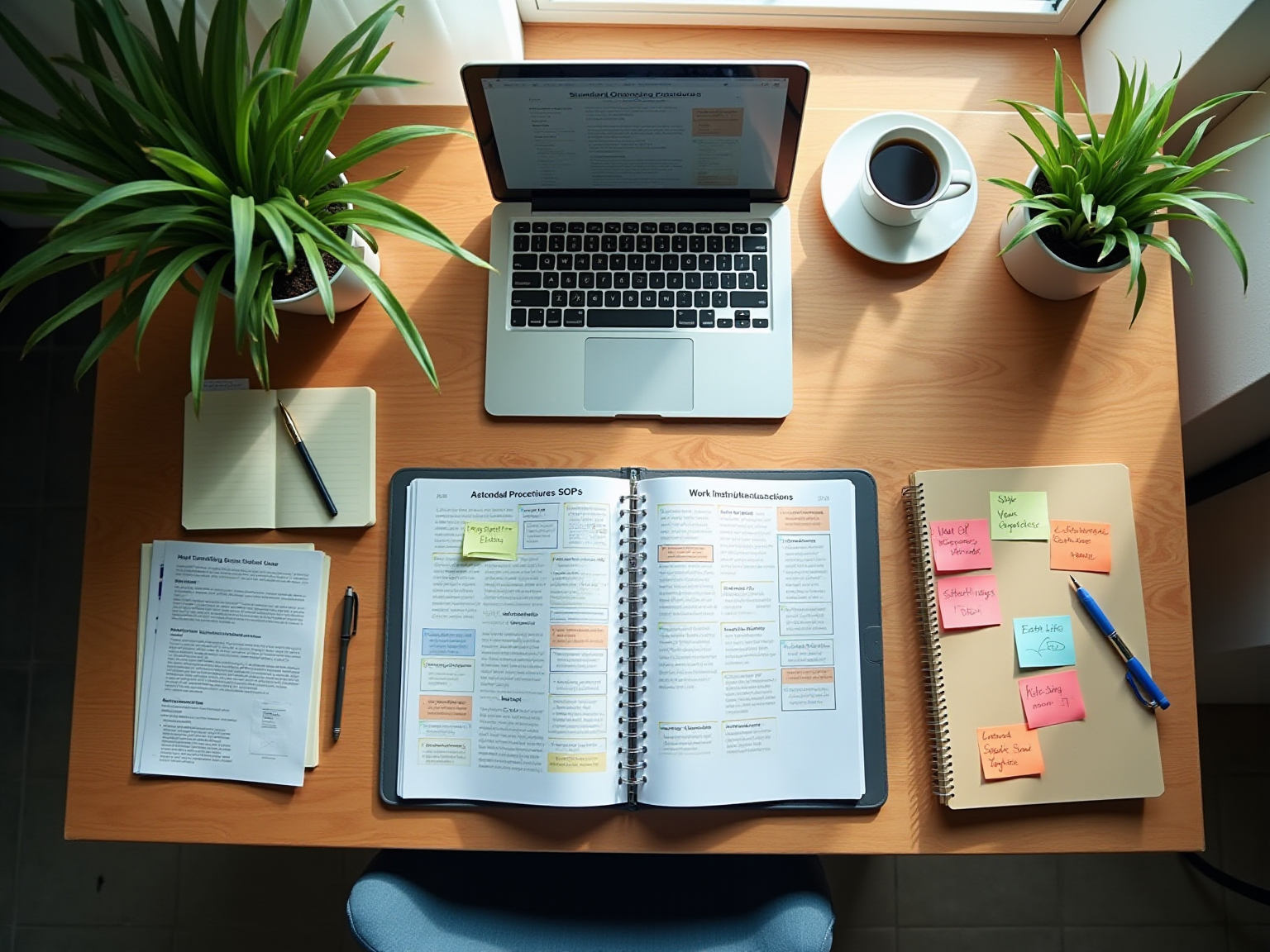
Process Improvement through Documentation
|
July 15, 2025
|
SOP vs Work Instruction: Key Differences and Use Cases Explained
Overview
You might be wondering what sets Standard Operating Procedures (SOPs) apart from Work Instructions. Well, the key differences really come down to their scope and detail.
- SOPs give you a broader overview of processes, while
- Work Instructions zoom in on specific tasks.
This distinction is super important!
- SOPs are essential for compliance and training in various industries, and
- on the flip side, Work Instructions help boost accuracy and efficiency in getting those tasks done.
Together, they play complementary roles in making operations run smoothly. So, next time you think about documentation, remember how these two work hand in hand to improve effectiveness!
Key Highlights:
- Standard Operating Procedures (SOPs) are formal documents outlining steps for executing tasks, ensuring consistent performance and compliance.
- Work Instructions are detailed guides focusing on specific tasks, providing step-by-step instructions to enhance accuracy and efficiency.
- SOPs cover broader processes, while Work Instructions focus on the specifics of individual tasks.
- The SOP Management Market is expected to grow at a CAGR of 11.25% from 2024 to 2031, indicating increased organizational reliance on these tools.
- Key players in the SOP Management Market include DocuSign, ServiceNow, SAP, Oracle, and others.
- SOPs are essential for regulatory compliance, training, and quality assurance in industries like healthcare and manufacturing.
- Work Instructions are beneficial for technical tasks, manufacturing processes, and customer service interactions.
- Effective documentation can reduce decision-making bottlenecks and improve operational efficiency.
- Organizations that implement SOPs often see enhanced training outcomes and compliance adherence.
Introduction
In the intricate world of organizational management, you might be wondering how clarity in processes can really make or break operational success. Standard Operating Procedures (SOPs) and Work Instructions are pivotal tools that play distinct yet complementary roles in boosting efficiency and compliance across various industries.
- SOPs give you a high-level overview of processes, making sure that everyone on the team is aligned and informed.
- On the other hand, Work Instructions dive into the specifics, guiding employees through the precise steps of individual tasks.
As organizations start to realize just how important these documentation strategies are, understanding when and how to use each one can lead to some serious improvements in productivity and quality assurance. With the Standard Operating Procedure Management Market expected to grow, effective documentation has never been more crucial.
So, let’s explore the nuances between SOPs and Work Instructions, highlighting their unique features, benefits, and practical applications across diverse sectors.
Defining Standard Operating Procedures and Work Instructions
You might be wondering what Standard Operating Procedures (SOPs) really are. Well, they’re formal documents that lay out the necessary steps to execute specific tasks or processes within an organization. Think of them as essential guidelines that help ensure consistent performance and compliance with industry regulations. SOPs usually cover broader processes, detailing responsibilities, required resources, and expected outcomes, which is important when considering the differences in SOP vs work instruction.
These are your detailed, step-by-step guides that provide explicit instructions on how to perform individual tasks. They tend to be more detailed than SOPs, focusing on the 'how' instead of the 'what' or 'why.' Work Instructions are designed to help employees carry out tasks accurately and efficiently, often including visuals or diagrams to make things clearer.
The comparison of SOP vs work instruction illustrates how they collectively create a strong documentation strategy that boosts operational efficiency and consistency in organizations. Did you know that the Standard Operating Procedure Management Market is projected to grow at a compound annual growth rate (CAGR) of 11.25% from 2024 to 2031? This just shows how much organizations are relying on these tools. Interestingly, as the number of workers on a farm increases, so does the presence of SOPs, highlighting their crucial role in managing larger teams effectively, especially in fields like agriculture.
Take, for example, the case of FlowForma’s adoption of AI-driven automation at Dresser Natural Gas Solutions. This shows the transformative impact of SOPs. By streamlining workflows, organizations can cut down on manual intervention and reduce human errors, which ultimately boosts compliance and process efficiency.
It’s clear that there’s a growing recognition of how important SOPs vs work instruction are in driving operational excellence across various industries, with key players in the Standard Operating Procedure Management Market including:
- DocuSign
- ServiceNow
- SAP
- Oracle
- Nintex
- K2 Blackpearl
- ProcessMaker
This highlights a competitive landscape that emphasizes the need for efficient record-keeping strategies. Plus, tools like SowFlow’s intuitive documentation solutions are designed to help organizations develop and manage their SOPs vs work instruction, which enhances operational efficiency and ensures teams can easily access the information they need.
Contrasting Features: SOPs vs. Work Instructions
When you start comparing SOPs and work instructions, a few key features really pop out:
- Scope: SOPs cover a wider range of processes, giving you a big-picture view of how different tasks fit together in the organization. On the flip side, work instructions zoom in on specific tasks, laying out the exact steps you need to follow to get things done.
- Detail Level: Standard operating procedures give you that high-level perspective, often wrapping multiple tasks into one process. Work instructions, however, get into the nitty-gritty of a single task, often including diagrams or screenshots to make things crystal clear.
- Audience: SOPs are mainly for managers and team leaders who need to understand the overarching processes, while work instructions are tailored for frontline employees who are the ones actually doing the work.
- Format: Typically, SOPs are formal documents with sections for purpose, scope, and responsibilities. In contrast, task guidelines are more straightforward, focusing on step-by-step instructions.
These differences highlight the unique roles each document plays in an organization, addressing various needs and audiences. You might be wondering why this matters. Well, recent trends show that organizations are recognizing how vital both SOP vs work instruction are in boosting operational efficiency. For example, statistics reveal that SOPs provide structured frameworks for cross-functional workflows, which can really amp up consistency and productivity.
A case study titled 'Creating Effective SOPs and Work Instructions' emphasizes that understanding the differences in SOP vs work instruction can lead to better consistency and efficiency in operations. As Iryna Smuk wisely noted, 'Therefore, only you can decide what functions best for your organization regarding SOP vs work instruction.' This is a crucial insight for operations managers; they need to evaluate their specific needs when choosing between these records to ensure they align with their organization's goals, culture, and task requirements. Plus, tools like Scribe Pages can help you put together detailed task guidelines with clear steps, making the documentation process even smoother.
Evaluating Benefits: When to Use SOPs and Work Instructions
You might be wondering when to use SOP vs work instruction in your organization. Well, it really depends on what you need! SOPs are your go-to for maintaining consistency across various tasks and processes, especially in complex operations that need to meet regulatory standards. Industries like healthcare, manufacturing, and food services really benefit from these structured frameworks. They help employees navigate compliance requirements and serve as fantastic training tools for onboarding new hires. With SowFlow, creating and updating SOPs is a breeze, allowing teams to keep their documentation fresh in a fast-paced business world. As Leapin' Lizard Labels puts it, SOPs promote positive change, cut down on quality variations, and ensure consistency—crucial elements in compliance-heavy environments.
Now, let’s dive into when to utilize guidelines. Guidelines are perfect for those regular tasks that need precise execution. They shine in repetitive environments, like assembly lines or technical support, where clarity and accuracy are key. By providing step-by-step guidance, work directives help employees carry out their tasks accurately and effectively, reducing mistakes and boosting productivity. SowFlow’s immediate record-keeping solution simplifies the development of SOP vs work instruction documents, enabling teams to share knowledge quickly and efficiently. Recognizing when to use each SOP vs work instruction can significantly enhance operational efficiency and employee performance. For example, organizations that implement SOPs often see better training outcomes and compliance adherence. Did you know that only 27% of small farms with two employees have written SOPs? That’s a huge opportunity for improvement in record-keeping, especially in compliance-heavy sectors where organized processes are a must. Plus, case studies show that having set procedures can reduce decision-making bottlenecks, streamline workflows, and ultimately enhance daily operational efficiency, cut costs, and improve productivity. As Anastasia Masadi, a Product Owner, puts it, 'SowFlow has been a game changer in the way we record tasks and deliver to our clients.' This really highlights how effective documentation solutions can transform your operations.
Identifying Use Cases: Choosing Between SOPs and Work Instructions
Identifying the right use case for SOP vs work instruction can really streamline your processes and boost efficiency. You might be wondering how exactly these tools can help you out. Let’s break it down!
-
Use Cases for SOPs:
- Regulatory Compliance: If you're in industries like pharmaceuticals or food production, you know how crucial it is to stick to regulations. SOPs are your best friends here, as they help document compliance processes. A solid SOP program can make a world of difference, enhancing your ability to maintain compliance with structured, repeatable processes. This means better consistency, less reliance on memory, and smoother audits. Plus, did you know that nearly one-third of enterprises have faced fraud or financial crime recently? That’s why having strong procedures is key. With SowFlow, creating and updating SOPs is a breeze, ensuring they stay relevant and effective for compliance.
- Training and Onboarding: Now, let’s chat about new hires. SOPs give them a clear understanding of your processes, making onboarding a lot smoother. Statistics show that 83% of workers believe having an onboarding program is beneficial. That’s a big deal! SowFlow’s user guide creation tools make it easy to whip up onboarding materials quickly, enhancing the overall training experience.
- Quality Assurance: Maintaining quality standards is vital, right? SOPs ensure everyone follows the same procedures, which is essential for organizations that want to uphold their reputation. With SowFlow, updating your quality assurance documentation is super simple, allowing for continuous improvement in your processes.
-
Use Cases for Work Instructions:
- Technical Tasks: If you’re in IT support, work instructions can guide your technicians through troubleshooting steps for specific issues. This ensures efficient problem resolution and minimizes downtime. With SowFlow’s instant documentation capabilities, you can quickly update these instructions to keep them aligned with the latest procedures.
- Manufacturing: On the production floor, work instructions are a must. They ensure that precise steps are followed to maintain product quality. This structured approach helps prevent errors and boosts productivity. SowFlow’s tools allow manufacturers to create and revise work instructions effortlessly, adapting to any changes in production processes.
- Customer Service: Ever thought about how work instructions can help customer service reps? They can guide them in handling specific inquiries or complaints effectively, leading to happier customers and increased loyalty. With SowFlow, your customer service teams can keep documentation up-to-date, enhancing their ability to respond to customer needs promptly, particularly when evaluating SOP vs work instruction for different tasks. This ultimately enhances your operational efficiency and compliance. So, what are you waiting for? Let’s get started!
Conclusion
You might be wondering about the difference between Standard Operating Procedures (SOPs) and Work Instructions, and why it even matters. Well, understanding this distinction is crucial for organizations looking to boost their operational efficiency and compliance. SOPs give you that big-picture view of processes, ensuring everyone’s on the same page and that industry regulations are met. They’re not just guidelines for consistent performance; they also double as handy training tools for newcomers. On the flip side, Work Instructions dive into the nitty-gritty details of specific tasks, helping frontline employees carry out their responsibilities with precision and confidence.
Now, when you combine both SOPs and Work Instructions, you’re setting your organization up with a solid documentation strategy that meets various operational needs. It’s exciting to see how these tools are gaining traction, as highlighted by the projected growth in the Standard Operating Procedure Management Market. This trend really underscores the rising value of structured documentation in streamlining workflows, cutting down on errors, and boosting overall productivity across different sectors.
Ultimately, using SOPs and Work Instructions effectively can lead to some serious improvements in quality assurance and compliance. Organizations that grasp when and how to use each type of documentation are in a great position to achieve operational excellence. As industries continue to evolve and face new challenges, making these strategies a priority will be key to maintaining a competitive edge and securing long-term success. So, what do you think? Are you ready to explore how these tools can transform your organization?
Frequently Asked Questions
What are Standard Operating Procedures (SOPs)?
Standard Operating Procedures (SOPs) are formal documents that outline the necessary steps to execute specific tasks or processes within an organization. They serve as essential guidelines to ensure consistent performance and compliance with industry regulations.
How do SOPs differ from Work Instructions?
SOPs cover broader processes and detail responsibilities, required resources, and expected outcomes, while Work Instructions are detailed, step-by-step guides that provide explicit instructions on how to perform individual tasks. Work Instructions focus more on the 'how' rather than the 'what' or 'why.'
Why are SOPs and Work Instructions important for organizations?
SOPs and Work Instructions create a strong documentation strategy that boosts operational efficiency and consistency. They help organizations manage tasks accurately and efficiently, reducing human errors and enhancing compliance.
What is the projected growth rate of the Standard Operating Procedure Management Market?
The Standard Operating Procedure Management Market is projected to grow at a compound annual growth rate (CAGR) of 11.25% from 2024 to 2031.
How do SOPs relate to team management in agriculture?
As the number of workers on a farm increases, the presence of SOPs also increases, highlighting their crucial role in effectively managing larger teams, especially in fields like agriculture.
Can you provide an example of the impact of SOPs in organizations?
An example is FlowForma’s adoption of AI-driven automation at Dresser Natural Gas Solutions, which shows how SOPs can streamline workflows, reduce manual intervention, and minimize human errors, ultimately boosting compliance and process efficiency.
Who are some key players in the Standard Operating Procedure Management Market?
Key players in this market include DocuSign, ServiceNow, SAP, Oracle, Nintex, K2 Blackpearl, and ProcessMaker.
What tools can help organizations manage their SOPs and Work Instructions?
Tools like SowFlow’s intuitive documentation solutions are designed to help organizations develop and manage their SOPs and Work Instructions, enhancing operational efficiency and ensuring easy access to information.
👍
What others are liking
5 Steps to outline your ideal documentation structure
5 MINS READ
Where to start the your journey of mapping out your ideal documentation structure, aligning it with the very heartbeat of your organization?
Defining a winning level of detail in your process
3 MINS READ
What is too much detail, and what is too little? This article described in that winning level detail about what detail is enough.