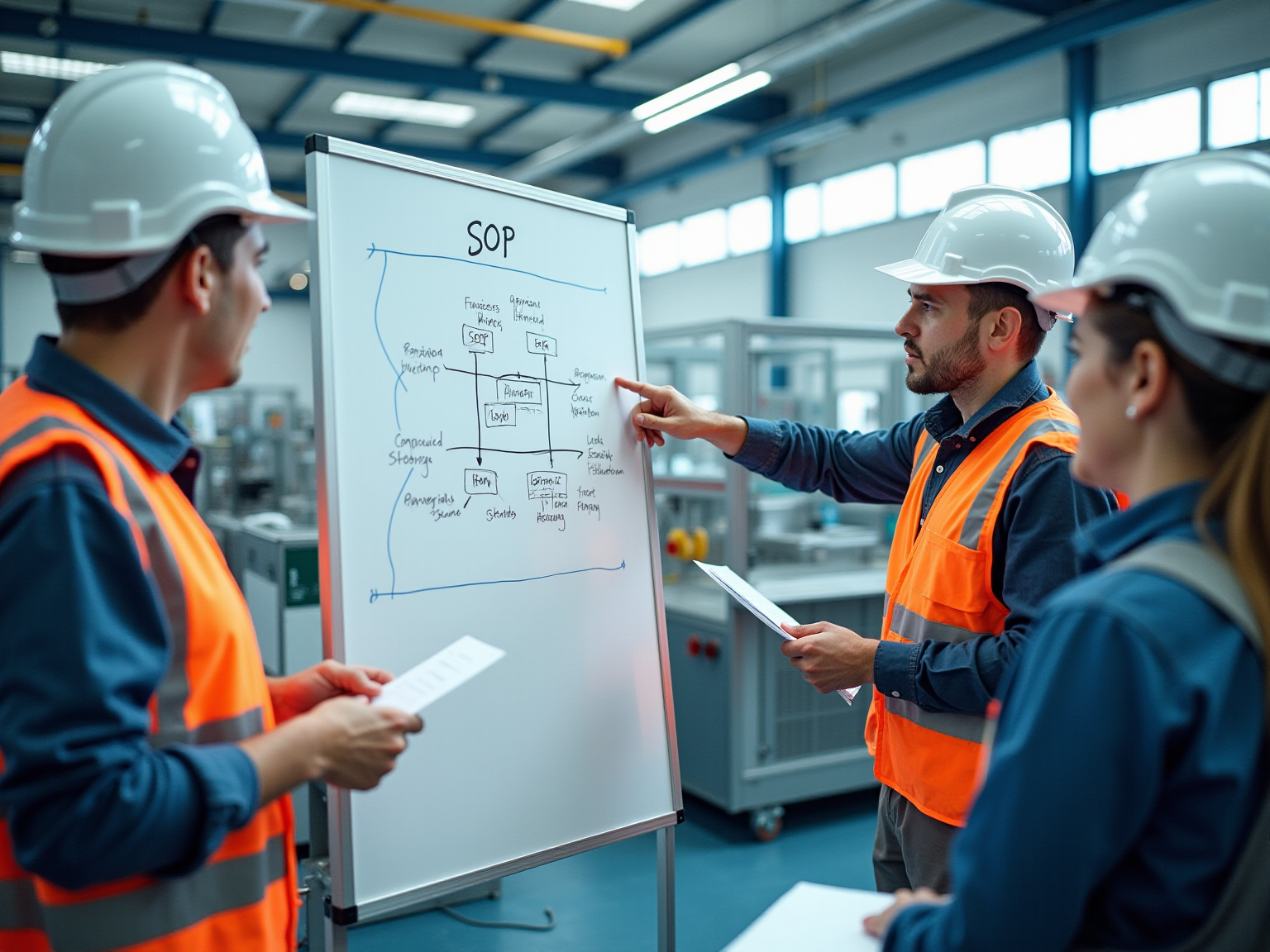
Overview
You might be wondering why Standard Operating Procedures (SOPs) are such a big deal in manufacturing. Well, let’s dive into it! This article highlights nine key benefits of implementing SOPs, all aimed at achieving operational excellence.
For starters, SOPs can really enhance efficiency and even cut down training time by about 30%! That’s a significant saving, right?
Plus, they help ensure regulatory compliance and boost product quality. It’s all backed by evidence showing that well-documented processes not only lead to better communication within teams but also result in substantial cost savings.
So, if you’re looking to streamline your operations, SOPs might just be the answer you need!
Key Highlights:
- SowFlow provides an intuitive platform for creating and updating SOPs efficiently in manufacturing.
- Digital SOPs enhance accessibility, allowing employees to access up-to-date procedures anytime, reducing errors.
- Implementing SOPs can reduce training time by an average of 30%, facilitating quicker onboarding of new employees.
- SOPs help ensure regulatory compliance by providing clear guidelines that align with industry standards.
- Standardized procedures foster better communication and collaboration among teams, leading to improved operational efficiency.
- SOPs are crucial for identifying and eliminating inefficiencies, potentially increasing operational performance by up to 30%.
- Maintaining SOPs contributes to consistent product quality, reducing defect rates and enhancing customer satisfaction.
- Effective SOP management can lead to significant cost savings by minimizing errors and waste in manufacturing processes.
- SOPs play a vital role in knowledge retention, ensuring that critical operational insights are preserved during employee transitions.
- Well-documented processes support operational scalability, allowing organizations to grow without compromising quality or efficiency.
Introduction
In the ever-changing world of manufacturing, you might be wondering how to achieve operational excellence. Well, it all comes down to effectively implementing Standard Operating Procedures (SOPs). As companies look to boost efficiency, cut down on errors, and stay compliant, innovative tools like SowFlow are stepping up as real game changers. They make creating and managing SOPs a breeze!
Let’s dive into the many perks of going digital with your SOPs. Imagine improving accessibility, speeding up onboarding, and fostering better teamwork—all while ensuring you meet regulatory requirements. By using advanced documentation tools, manufacturing teams can keep essential operational insights intact and even save on costs while scaling up. So, why not explore how a structured approach to SOPs can revolutionize your manufacturing operations and set the stage for sustainable growth in a competitive landscape?
SowFlow: Streamline SOP Creation for Enhanced Efficiency
You might be wondering how to make the development of SOP in manufacturing easier. Well, SowFlow has got you covered with an intuitive platform designed just for that! By leveraging advanced technology, teams can quickly document their processes, ensuring that SOPs are not only created efficiently but also kept up to date. This streamlined approach means less time spent on documentation and more focus on what really matters—your essential operational tasks.
Imagine transforming those complex processes into clear, step-by-step guides. Sounds great, right? That's exactly what SowFlow does, enhancing productivity and minimizing errors in manufacturing operations. Plus, effective standard operating procedures have been shown to boost customer satisfaction and maintain inventory accuracy. Just look at case studies like the Customer Product Return Process for proof!
As we look ahead to 2025, the advantages of SOP in manufacturing have become clearer than ever. Organizations are increasingly turning to digital documentation tools to ramp up productivity and operational efficiency. Remember what Idowu Koyenikan said? "If you look at anything successful, you will find traces of a good leader in it." This really highlights how important leadership is in effectively executing SOP in manufacturing.
Now, let’s dive into the future of manufacturing! It hinges on turning data into actionable insights through statistical methods, which underscores the need for teamwork in developing efficient procedures. After all, "Unity is strength…when there is teamwork and collaboration, wonderful things can be achieved." And don’t forget, federated learning across manufacturing sites will not only enhance model robustness but also safeguard proprietary process information. This showcases just how much the industry is evolving!
Digital SOPs: Improve Accessibility and Update Speed
You might be wondering how Digital Standard Operating Procedures (SOPs) can really make a difference in your workplace. Well, they significantly enhance accessibility and update speed, allowing employees to access critical information anytime, anywhere. With advanced digital record-keeping tools, organizations can ensure that everyone on the team has the most up-to-date procedures at their fingertips. This not only minimizes the risk of errors from outdated information but also fosters a culture of continuous improvement, enabling teams to quickly adapt to changes in processes or regulations.
Now, let’s dive into how easy it is to create these SOPs. The platform offers a straightforward process that lets teams develop user guides effortlessly—just a single command can pull up the knowledge they need. In the manufacturing sector, having access to digital SOP in manufacturing is crucial. Did you know that organizations using SowFlow's digital documentation see a noticeable increase in operational efficiency? They spend less time searching for information, which is a game changer. Plus, the ability to revise standard operating procedures, or sop in manufacturing, in real-time keeps employees updated on the latest practices—essential in today’s fast-paced environment.
Experts agree on the importance of digital SOPs for accessibility. They not only streamline operations but also enhance compliance with industry standards by implementing sop in manufacturing. Colin Kelley put it perfectly when he said, "It has genuinely professionalized the experience of utilizing our services," highlighting how effective records can transform operations.
As we move through 2025, the trend towards digital records is only growing. Organizations are realizing the need for agile and responsive systems that drive operational excellence. By embracing SowFlow's innovative solutions, you can turn your documentation processes into comprehensive how-to guides, ensuring every team member has what they need to succeed. To really maximize the benefits of digital SOPs, companies should focus on regular updates and training to keep everyone informed and engaged. So, are you ready to take the leap into a more efficient future?
Reduced Training Time: Accelerate Onboarding Processes
You might be wondering how implementing SOP in manufacturing can truly make a difference in training new employees. Well, let me tell you, it can significantly streamline the process! By providing clear, standardized instructions, new hires can quickly get the hang of their roles with minimal supervision. This structured approach not only speeds up onboarding but also ensures that employees have the essential knowledge to perform their tasks effectively right from day one. As a result, organizations can see productivity levels soar sooner, which means lower overall training costs.
Now, here’s something interesting: statistics show that companies using SOPs can reduce training time by an average of 30%. That’s a big win! This allows teams to focus on operational excellence instead of getting bogged down in repetitive training sessions. Take Marsh McLennan, for example. Their use of digital tools to enhance employee well-being led to improved productivity and job satisfaction for over 20,000 employees. This really highlights the positive impact of efficient onboarding procedures, especially when the SOP in manufacturing is included in the training mix.
But it doesn’t stop there! Experts point out that SOPs aren't set in stone; they evolve over time. By incorporating feedback from staff, training materials can be continuously refined and enhanced. This adaptability means that new hires get the most relevant and effective instructions, which cuts down the time it takes for them to become fully operational. Speaking of which, there’s this fantastic platform that’s been a game changer. It lets teams create SOPs and training materials on the fly without needing to capture separate screenshots or exit the browser. As Anastasia Masadi, a Product Owner, put it, "SowFlow gave me time from my life back," which really emphasizes how these time-saving features boost productivity.
In a world where only 29% of new hires feel adequately supported—thanks to Gallup for that statistic—the implementation of standardized instructions can really bridge that gap. It fosters a more confident and capable workforce. Remember the saying, "Unity is strength…when there is teamwork and collaboration, wonderful things can be achieved"? This perfectly captures the cooperative spirit of executing SOP in manufacturing and their positive effect on team dynamics.
Regulatory Compliance: Ensure Adherence to Industry Standards
You might be wondering why SOP in manufacturing is such a big deal. Well, they’re essential for keeping everything in line with regulations. By laying out clear and detailed guidelines that match industry standards, organizations can really cut down on the chances of non-compliance. This is especially important in environments where safety and quality are absolutely non-negotiable. Did you know that 67% of global executives think the complexity of ESG regulations is a huge challenge? This just goes to show how crucial it is to have solid SOPs to navigate these requirements effectively.
Speaking of tools, SowFlow has some great options that help companies quickly update their SOPs when regulations change. This means they can stay compliant and avoid those costly penalties. Compliance experts have noticed that 57% of their roles have become more specialized, which points to the increasing importance of keeping accurate records to meet industry standards. This specialization calls for a more organized approach to SOP in manufacturing management, ensuring that documentation is not only spot-on but also easy to access. About 27% of security and IT professionals mention internal audit fatigue as a significant compliance hurdle. But here’s the good news: well-structured SOPs can help lighten that load by streamlining processes and bringing clarity to the table.
The impact of SOP in manufacturing on compliance with industry standards is enormous. They not only help manufacturing companies meet regulatory requirements but also foster a culture of SOP in manufacturing and ongoing improvement. As organizations work to boost their compliance strategies, integrating effective SOP in manufacturing becomes essential for protecting against potential vulnerabilities. For example, case studies have shown gaps in regular compliance auditing practices, which can be addressed by implementing comprehensive SOPs in manufacturing.
To really drive home the risks of non-compliance, consider this: 98% of organizations have a connection with at least one third-party that has faced a breach in the past two years. That’s a stark reminder of the potential fallout from poor record-keeping and compliance practices. By leveraging the solutions available, businesses can keep their documentation relevant and up-to-date, ultimately driving operational excellence. So, operations managers, why not take advantage of SowFlow's tools to create and maintain effective procedures? This way, your teams will be well-prepared to meet industry standards and regulatory requirements.
Enhanced Communication: Foster Team Collaboration
You might be wondering how SOP in manufacturing can really make a difference in your team’s communication. Well, they play a crucial role by creating a common framework for everyone involved through the implementation of SOP in manufacturing. When team members follow the SOP in manufacturing, misunderstandings and miscommunications drop significantly, paving the way for a more collaborative environment. For example, a leading telecommunications provider in Indonesia saw an impressive 67% reduction in operational delays and a whopping 250% increase in on-time deliveries after rolling out standardized processes. This shift didn’t just streamline operations; it also boosted team communication and collaboration, which is in line with the SOP in manufacturing. As the Chief Financial Officer pointed out, "Renoir has been able to identify and help implement several improvements in the respective processes that have significantly helped the company strengthen its position in the market."
Now, let’s talk about the tools that make developing and sharing SOPs a breeze. They ensure that all team members are on the same page and fully informed about necessary processes. Anastasia Masadi, a Product Owner, shares her excitement: 'This platform has been a game changer in the way we document work and deliver to our clients.' She adds, "I no longer need to take each screenshot separately, and I can create SOPs and training materials without leaving the browser. SowFlow has truly given me time back in my life." This kind of clarity not only improves teamwork but also boosts overall efficiency. Statistics show that organizations implementing SOP in manufacturing notice a significant uptick in communication, with teams reporting a 30% rise in collaborative efforts. So, if you’re looking to enhance your team’s communication and foster operational excellence, utilizing standard operating procedures is definitely the way to go!
Process Improvement: Identify and Eliminate Inefficiencies
You might be wondering why SOP in manufacturing is such a big deal. Well, they’re essential for spotting and cutting out inefficiencies. By carefully documenting workflows, organizations can take a closer look at each step and uncover opportunities for improvement. Take Adam Afrique, a soap producer in Ivory Coast, for instance. They boosted their production efficiency with prompt remote maintenance, showing how organized records can prevent downtime and fuel growth.
Now, let’s talk about how an information system can really amp up a team’s ability to regularly assess and tweak their SOPs. This ensures that procedures stay efficient and organized. With SowFlow, creating user guides is a breeze! Teams can access their documentation with just a single command, which cuts down on unnecessary meetings and keeps everything relevant in our fast-paced business world. This commitment to continuous improvement not only ramps up productivity but also fosters a culture of excellence in operations. Did you know that organizations that regularly review their SOPs can see efficiency gains of up to 30%? That’s a significant boost in operational performance, which ultimately leads to better results and lower costs.
Speaking of efficiency, industry leaders are all about that lean approach, where every resource is aimed at delivering more value to customers. As W. Edwards Deming famously said, "Change is inevitable, but resistance to change is a constant." By leveraging standard operating procedures in manufacturing and a quick record-keeping solution, teams can systematically pinpoint inefficiencies, streamline their operations, and enhance overall productivity. This sets the stage for sustainable growth and success in a competitive landscape.
So, how do you effectively implement or review SOPs? Operations managers should set a regular schedule for evaluations, making sure all team members are involved and that documentation reflects current practices. Plus, with SowFlow’s features, updating user guides is quick and easy, ensuring everyone has instant access to the most relevant information. Let’s keep the conversation going about how we can make our operations even smoother!
Quality Control: Maintain Consistent Product Standards
Implementing SOP in manufacturing is super important for ensuring that product quality remains consistent. You might be wondering why that is. Well, by standardizing processes, organizations can really cut down on variability and defects, which leads to more reliable products. Research shows that companies that adopt SOP in manufacturing experience a significant drop in defect rates—some even report improvements of up to 30% in product consistency! Plus, the creative tools from this company help producers craft detailed SOPs that lay out quality control strategies at every stage of production.
As Anastasia Masadi, a Product Owner, puts it, "SowFlow has transformed the way we document work and deliver to our clients. I can develop standard operating procedures and training materials without capturing individual screenshots or exiting the browser, allowing me to regain precious time in my life." This structured approach, incorporating SOP in manufacturing, not only boosts product reliability but also builds customer trust and satisfaction.
Now, let’s talk about expert opinions. They really emphasize how critical the SOP in manufacturing is for maintaining product standards. A quality control expert once said, "Quality is not what happens when what you do matches your intentions. It is what happens when what you do matches your customers’ expectations." This really drives home the point that aligning practices with customer needs is key, and it’s totally achievable through effective SOP in manufacturing.
Speaking of that, there’s a case study called 'Quality Excellence as a Habit' that shows organizations committed to continuous improvement through SOP in manufacturing can achieve a better balance between short-term wins and long-term quality goals. By fostering a culture of quality excellence, these companies not only ramp up their efficiency but also ensure sustainable quality initiatives that resonate with their customers. This dedication to quality is reflected globally, as Pro QC offers solutions in over 88 countries, showcasing the widespread importance of SOP in manufacturing for achieving consistent product standards.
In summary, incorporating SOP in manufacturing isn’t just a box to check; it’s a strategic move that can really impact product quality and operational excellence. As Will Durant wisely said, quality excellence is a continuous habit, highlighting the need for ongoing dedication to quality initiatives. If you're curious about how this platform can enhance your SOP creation process, why not schedule a demonstration today?
Cost Savings: Minimize Errors and Waste
You might be wondering how SOP in manufacturing can really make a difference in the industry. Well, they’re absolutely pivotal in driving significant cost savings by cutting down on errors and waste. When processes are clearly defined, the chances of mistakes drop, which means less rework and reduced scrap materials. By using advanced documentation tools, organizations can whip up precise SOPs that guide employees through each task, ensuring that resources are used optimally.
Speaking of tools, SowFlow offers some fantastic functionalities like instant document generation and efficient organization. Imagine being able to pull answers from documents in seconds! This not only boosts knowledge management but also ramps up overall efficiency. It’s a structured approach that not only slashes operational costs but also enhances profitability.
Now, let’s talk about some real-world examples. Organizations that have embraced best practices in SOP management often find themselves more agile and responsive to operational challenges, which leads to improved efficiency. Did you know that effective SOP in manufacturing can lead to cost savings of up to 30% in operations? That’s a significant impact just from reducing errors and waste! Plus, companies that stick to clear SOPs around brand guidelines not only protect their brand integrity but also streamline their processes, helping with cost efficiency.
And here’s something interesting: with 8,500 people already signed up to get expert advice on unlocking growth, it’s clear there’s a growing interest in effective SOP management solutions. This platform also provides specialized customer success representatives and training in organizational best practices, ensuring businesses can create a solid record management system. In summary, incorporating well-designed SOP in manufacturing, supported by comprehensive documentation capabilities, is crucial for manufacturing companies looking to boost efficiency and achieve substantial cost savings. So, why not explore these solutions further?
Knowledge Retention: Preserve Critical Operational Insights
You might be wondering why SOP in manufacturing matters so much for companies. Well, they’re key for keeping knowledge alive and kicking! Think of them as a treasure trove of essential insights that ensure vital information is always at hand, even when employees move on or retire. By documenting processes on a platform, organizations can build a solid knowledge base that new hires can easily tap into, making transitions smoother and keeping operations running like a well-oiled machine.
Speaking of keeping things running, SowFlow's instant documentation solution makes creating and updating user guides a breeze. This means your documentation stays relevant in our fast-paced business world. And let’s face it, preserving knowledge is crucial for maintaining efficiency and effectiveness in the SOP in manufacturing.
Now, let’s talk about onboarding. Effective knowledge management practices can really turbocharge the onboarding process, helping new employees get up to speed quickly with the info they need to succeed. Did you know that organizations with a strong SOP in manufacturing see higher knowledge retention rates? That’s right! This often translates to better performance. Companies that implement organized procedures, such as an SOP in manufacturing, typically report a significant drop in training and onboarding time, leading to a more agile workforce.
There are plenty of success stories out there showcasing how standard procedures have kept functional insights intact. For instance, one manufacturing company revamped its onboarding process with well-documented procedures and a SOP in manufacturing, achieving a whopping 30% reduction in training time and a smoother transition for new hires. This not only boosted employee satisfaction but also ramped up overall productivity.
Industry leaders really emphasize how important SOP in manufacturing is for ensuring operational continuity, especially during employee transitions. As one industry expert put it, 'Effective SOP in manufacturing is essential for ensuring that knowledge is retained and that operations run smoothly, even as personnel change.' This really highlights the need for organizations to focus on knowledge retention through smart record-keeping strategies. By using this platform, manufacturing firms can ensure that performance insights are preserved in their SOP in manufacturing, paving the way for lasting excellence in their operations. So, why not consider asking for an invitation today to see how this platform can transform your record-keeping approach?
Operational Scalability: Support Growth Without Compromise
You might be wondering how SOP in manufacturing can really make a difference. Well, let me tell you—they're absolutely essential for achieving operational scalability! As organizations grow, having well-documented processes allows new teams or locations to replicate what works without losing quality or efficiency. In fact, did you know that 80% of organizations hit roadblocks due to outdated digital technologies? That’s a real bummer, especially when it highlights the urgent need for efficient documentation solutions, like those offered by various companies.
Speaking of that, Anastasia Masadi, a Product Owner, puts it perfectly: 'This platform has been a game changer in the way we document work and deliver to our clients.' Imagine not having to capture each screenshot individually or even exit your browser while creating SOPs and training materials! The service has given me time back in my life, and that’s a huge win.
This is where SowFlow’s user-friendly tools come into play. With features like automated screenshot capture and in-browser SOP creation, companies can easily update and distribute documents, keeping them relevant in our fast-paced world. This adaptability isn't just nice to have; it's crucial for sustaining growth and staying competitive in manufacturing. Plus, expert insights reveal that organizations with robust SOP in manufacturing enjoy significant scalability, enabling them to streamline processes and reduce those lengthy meetings we all dread. Yikes! This really underscores the need for effective documentation solutions. By implementing solid SOP in manufacturing—backed by success stories like XYZ Manufacturing, which boosted productivity by 30% after adopting SowFlow—manufacturing organizations can not only support their growth but also enhance overall operational excellence. So, what are you waiting for? Let’s dive into the world of effective documentation together!
Conclusion
You might be wondering how implementing Standard Operating Procedures (SOPs) can really make a difference in manufacturing organizations. Well, let me tell you, it’s a game changer! Digital SOPs, especially with platforms like SowFlow, offer a ton of benefits. They make creating and managing SOPs a breeze, so your processes become more accessible, and your teams can adapt quickly to any changes. This flexibility is super important for staying compliant with industry regulations and cultivating a culture of continuous improvement.
And that’s not all! Integrating SOPs can really speed up the onboarding process, cutting down on training time and costs. With clear, standardized instructions, new hires can jump in and start contributing much faster. Plus, your existing employees will appreciate the boost in communication and collaboration. The structured approach that SOPs provide helps minimize errors and waste, driving significant cost savings and allowing organizations to use their resources more effectively.
As you navigate the ever-changing manufacturing landscape, don’t underestimate the role SOPs play in preserving vital operational insights and supporting scalability. Keeping knowledge accessible ensures that companies can maintain continuity and efficiency, even as they grow. In today’s fast-paced environment, using innovative documentation tools like SowFlow is crucial for achieving sustainable growth and staying ahead of the competition.
So, in a nutshell, committing to effective SOP implementation isn’t just about following procedures; it’s a strategic advantage that can lead to greater productivity, better quality, and impressive cost reductions. Embracing this structured approach empowers manufacturing teams to flourish, ensuring they’re ready to tackle the challenges of an evolving industry.
Frequently Asked Questions
How can SowFlow make the development of SOP in manufacturing easier?
SowFlow provides an intuitive platform that allows teams to quickly document their processes, ensuring that SOPs are created efficiently and kept up to date, which helps save time on documentation and allows more focus on essential operational tasks.
What are the benefits of using digital SOPs in the workplace?
Digital SOPs enhance accessibility and update speed, allowing employees to access critical information anytime and anywhere. This minimizes errors from outdated information and fosters a culture of continuous improvement.
How does SowFlow improve operational efficiency in manufacturing?
Organizations using SowFlow's digital documentation tools experience increased operational efficiency by reducing the time spent searching for information and enabling real-time revisions of SOPs, keeping employees updated on the latest practices.
What impact do SOPs have on training new employees?
SOPs significantly streamline the onboarding process by providing clear, standardized instructions, allowing new hires to quickly understand their roles with minimal supervision, which can reduce training time by an average of 30%.
How do SOPs evolve over time?
SOPs are not static; they evolve through continuous feedback from staff, allowing training materials to be refined and enhanced, ensuring that new hires receive the most relevant and effective instructions.
What is the importance of teamwork in implementing SOPs?
Teamwork is crucial in executing SOPs effectively, as collaboration leads to improved processes and outcomes, fostering a cooperative spirit that enhances team dynamics and productivity.
Can you provide an example of a company that benefited from SOPs?
Marsh McLennan improved productivity and job satisfaction for over 20,000 employees by using digital tools to enhance employee well-being, highlighting the positive impact of efficient onboarding procedures that include SOP in manufacturing.
What role does leadership play in the execution of SOPs?
Effective leadership is essential for successfully implementing SOPs in manufacturing, as it guides the organization towards operational excellence and promotes a culture of accountability and continuous improvement.
👍
What others are liking
5 Steps to outline your ideal documentation structure
5 MINS READ
Where to start the your journey of mapping out your ideal documentation structure, aligning it with the very heartbeat of your organization?
Defining a winning level of detail in your process
3 MINS READ
What is too much detail, and what is too little? This article described in that winning level detail about what detail is enough.