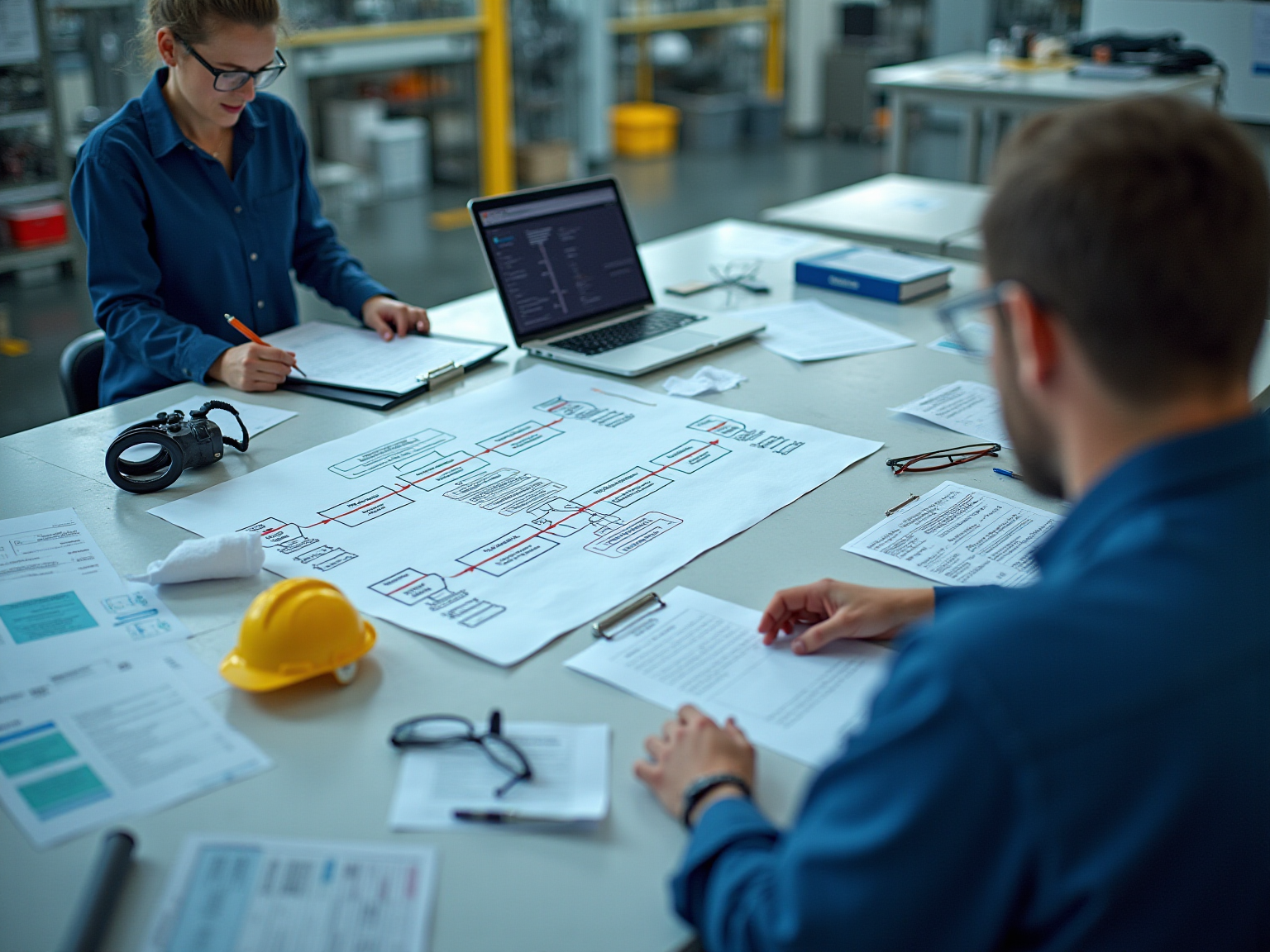
Overview
You might be wondering how to create effective manufacturing standard operating procedures (SOPs). Well, this article lays out a friendly seven-step process that emphasizes just how crucial SOPs are for ensuring consistency, efficiency, and compliance in your organization. It’s packed with practical steps like:
- Defining your objectives
- Engaging experts
- Testing your procedures
- Setting up regular reviews
Together, these steps really help foster operational excellence and keep the wheels of continuous improvement turning in your manufacturing practices. So, let’s dive in and explore how you can make your documentation work for you!
Key Highlights:
- Manufacturing SOPs are essential for ensuring consistent and efficient task execution, maintaining quality standards, and complying with regulations.
- Standardizing procedures can reduce variability, enhance safety, and boost productivity, leading to cost savings and improved operational efficiency.
- Defining the scope and objectives of an SOP is crucial for focusing on specific tasks and aligning with organizational goals.
- Engaging subject matter experts and gathering existing resources are key steps in creating effective SOPs.
- An effective SOP should have a clear format, incorporate visuals, and include safety precautions and quality control measures.
- Reviewing and testing the SOP with feedback from stakeholders ensures its practicality and relevance in real-world applications.
- Implementing SOPs requires comprehensive training and clear communication across teams to ensure understanding and adherence.
- Regularly reviewing and updating SOPs fosters a culture of continuous improvement and keeps the documentation aligned with best practices.
Introduction
In the world of manufacturing, you might be wondering just how crucial Standard Operating Procedures (SOPs) really are. Well, let me tell you—they're the backbone of keeping things running smoothly! These essential documents ensure that tasks are done with precision and that everything aligns with industry regulations. As companies look to boost productivity and uphold quality standards, crafting and implementing effective SOPs becomes a top priority.
So, what does that process look like? It involves:
- Defining the purpose and scope of the SOPs
- Gathering all the necessary information
- Conducting thorough reviews
It might sound intricate, but trust me, it’s worth it! This article will explore the key steps for creating SOPs that not only streamline workflows but also promote a culture of continuous improvement in manufacturing settings. By embracing best practices and tapping into expert insights, organizations can really transform their operations and achieve impressive efficiencies. Now, let’s dive into how you can make this happen!
Understand the Purpose of a Manufacturing SOP
You might be wondering what a manufacturing standard operating procedure (SOP) truly entails. Well, it's a crucial document that lays out the specific steps needed to carry out tasks consistently and efficiently. The main goal of an SOP is to ensure that everyone is on the same page, which helps maintain quality standards and meet industry regulations. As Shigeru Mizuno wisely said, 'Quality is not an act, it is a habit.' This highlights the need for ongoing improvement in quality, something that SOPs are designed to support.
By standardizing procedures, you can significantly reduce variability, enhance safety measures, and boost overall productivity. In fact, organizations that implement SOPs often see a drop in decision-making delays, streamlined workflows, and impressive cost savings—all while improving operational efficiency. Did you know that a Forrester study commissioned by Adobe found that a staggering 97% of companies had limited or no digital document procedures? This underscores the urgent need for effective manufacturing standard operating procedures in the current manufacturing landscape.
Take, for example, the case study titled "Established Procedures Enhance Operational Efficiency." It shows how well-defined processes can lead to lower costs and time savings, while also ramping up productivity. Understanding the purpose of SOPs is the first step toward creating effective documentation that aligns with your organization’s goals and supports your team’s performance.
If you’re an operations manager looking to implement effective SOPs, services like Whale can make documenting procedures and policies a breeze. So, why not explore how you can enhance your operations today?
Define the Scope and Objectives of Your SOP
Defining the scope of your Standard Operating Procedure (SOP) is super important for making it effective. You might be wondering where to start—well, begin by pinpointing the specific procedures that the SOP will cover. Think about the tasks that need standardization and which departments will be involved. Clearly stating the objectives of the SOP—like boosting efficiency, ensuring compliance, or enhancing safety—will help you focus on what really matters. This focus not only streamlines the development process but also gets all relevant stakeholders on board from the get-go.
Now, speaking of keeping things organized, statistics show that standard operating procedures should monitor changes over time. This means detailing previous versions and the reasons for any revisions, which really highlights why having a well-defined scope and objectives is key. By documenting these foundational elements early on, you create a guiding framework that acts as a clear reference throughout the SOP development journey. This approach not only sets you up for successful execution but also aligns with current trends that emphasize the need for clarity and adaptability in the manufacturing standard operating procedure. And let’s not forget, best practices for setting objectives in 2025 stress the importance of establishing measurable goals that can evolve with your organization, ensuring your SOP stays relevant and effective in a fast-paced business environment.
Gather Relevant Information and Resources
You might be wondering how to make your manufacturing standard operating procedure truly effective. Engaging with subject matter experts (SMEs) who have hands-on experience with the activities you're documenting is key. These experts can share insights that really enhance the clarity and accuracy of your documentation. Start by gathering existing resources, like previous SOPs, training materials, and workflow diagrams. These will serve as the building blocks for your new SOP. And don’t forget to watch the activities in action! This step is crucial because it helps you spot subtleties and differences that might not show up in written documents.
Now, let’s talk about resources. Be sure to collect all the necessary tools, equipment, and safety guidelines to ensure your SOP is thorough and practical. This kind of research is vital. Did you know that a lack of process documentation can cost Fortune 500 companies up to $12 billion a year? By tapping into the expertise of SMEs and leveraging current documentation, you can create SOPs that not only reflect best practices but also drive operational success. Regularly evaluating these SOPs, as highlighted in various case studies, allows for ongoing refinement and optimization. This way, you can ensure they meet their intended goals and boost overall efficiency.
Write the Standard Operating Procedure
When it comes to crafting an effective manufacturing standard operating procedure, you’ll want to kick things off with a clear and consistent format. You might be wondering where to start—well, a descriptive title that captures the essence of the procedure is a great first step, followed by an introduction that lays out its purpose and scope. To make things easy, use numbered steps to outline the procedure, ensuring each step is actionable and straightforward. And hey, incorporating visuals like flowcharts or diagrams can really boost understanding; did you know that the brain processes visual data in just 13 milliseconds? That’s pretty quick, right? It makes grasping complex information a whole lot easier.
Now, let’s not forget about safety precautions and quality control measures—these are essential for thoroughness. Speaking of that, with SowFlow, you can take advantage of templates and automated updates to create and revise your SOPs effortlessly, keeping them relevant in our ever-changing business world. Finally, be sure to review your document for clarity and conciseness, making any tweaks needed to align with your audience's needs. By having established manufacturing standard operating procedures in place, you’ll find that they can really minimize decision-making bottlenecks and streamline workflows, ultimately boosting the efficiency of your daily operations. So, are you ready to dive into the world of effective documentation?
Review and Test Your SOP for Effectiveness
So, you've created your SOP—now what? It's super important to loop in key stakeholders and subject matter experts for a thorough review. This teamwork helps gather valuable feedback about how clear and practical your document really is. Once you've made those revisions, it’s time for a pilot test in a controlled environment to see how effective the SOP is. During this phase, keep an eye on how well employees stick to the SOP and spot any challenges they might run into. This real-world testing is key because effective procedures need input from those actually doing the work to stay accurate and relevant.
You might be thinking, "Why is gathering feedback such a big deal?" Well, it’s not just a box to check off; it’s a crucial step that can really boost operational consistency. Take All Residential Real Estate, for example. They moved from paper checklists to a digital documentation system, and guess what? They saw improved efficiency and less need for expert help. This highlights just how important pilot testing and stakeholder feedback are for refining the manufacturing standard operating procedure.
Now, let’s talk about SowFlow. It’s changing the game for how teams document their work and deliver to clients. Anastasia Masadi, a Product Owner, put it perfectly: "I don’t have to take each screenshot separately, and I don’t even have to leave the browser while I’m developing the manufacturing standard operating procedure and training materials." SowFlow gave me time from my life back! By consistently integrating user feedback and tweaking the SOP, organizations can keep their documentation relevant and effective. SowFlow’s features make it easier to gather insights during the review and testing phases, leading to better performance and happier users.
Implement and Communicate the SOP Across Teams
You might be wondering how to implement the SOP effectively. Well, it all starts with organizing some comprehensive training sessions for your team. These sessions should clearly explain what the SOP is all about, guide everyone through the procedures, and, of course, address any questions or concerns that pop up. It's super important to distribute the SOP document widely—think of using digital platforms like an internal wiki or document management system. Plus, providing resources like templates and recommended readings can really enhance accessibility for everyone involved.
Encouraging feedback during these training sessions is vital. It helps pinpoint areas that might need a bit more clarification or adjustment. This proactive approach not only fosters a better understanding of the SOP but also boosts the chances of it being adopted and followed by your employees. Did you know that research shows teams investing in proper SOP training work smarter, faster, and with fewer disruptions? By integrating SOP training into actual workflows, employees are more likely to remember the information and apply it effectively, ultimately contributing to operational excellence.
Now, let’s dive into some examples. Learning platforms like SC Training offer effective strategies through bite-sized courses, helping organizations implement training that leads to a more skilled and committed workforce. To take your documentation and knowledge management systems to the next level, consider reaching out to SowFlow. They provide instant user guides and user-friendly tools, like customizable templates and interactive training modules, that can really streamline your SOP implementation.
Establish a Process for Regular Review and Updates
You might be wondering how to keep your manufacturing standard operating procedure relevant and effective. Well, implementing a structured review schedule is a great start—aim for once a year or even every six months. It’s a good idea to assign someone accountable to manage this process. They should be collecting user feedback and staying updated on any changes in regulations or industry standards. Each time you review, focus on checking your SOP for accuracy, relevance, and clarity. If you find anything that needs updating, make those changes and let all your employees know right away.
This ongoing enhancement strategy not only boosts the efficiency of your SOPs but also aligns them with best practices. Plus, it fosters a culture of adaptability within your organization. Frequent updates are key; organizations that prioritize this often see significant improvements in operational effectiveness and compliance. Did you know that a Forrester report commissioned by Adobe found that a whopping 97% of organizations have minimal or no digital document systems? That really highlights the common challenges out there regarding documentation, especially when it comes to the manufacturing standard operating procedure. For instance, companies that actively seek employee feedback and leverage operational data to refine their manufacturing standard operating procedures tend to align their documentation more closely with real-world applications. This leads to streamlined processes and less chaos in operations. By nurturing a culture of continuous improvement—like the one showcased in the case study titled 'Continuous Improvement of SOPs'—organizations can ensure that their SOPs stay effective, efficient, and in line with best practices. So, what’s stopping you from taking that next step?
Conclusion
You might be wondering why implementing Standard Operating Procedures (SOPs) is such a big deal. Well, it's not just a box to check; it’s a game changer for manufacturing operations! By grasping the purpose of SOPs, you can ensure that everything runs smoothly, with consistency, quality, and compliance across the board. When you define the scope and objectives, it sets the stage for targeted improvements that really align with your operational goals. Plus, gathering the right information and resources means your SOPs are based on solid ground and best practices.
Now, let’s talk about writing effective SOPs. It’s all about clarity and practicality, making it a breeze for employees to follow the established procedures. Don’t forget the review and testing phases—these are crucial! Engaging stakeholders and running pilot tests can give you insights that really boost the effectiveness of your documents. Once everything's in place, comprehensive training and clear communication are key to ensuring everyone understands and sticks to the plan. This leads to a noticeable bump in operational efficiency.
Speaking of keeping things fresh, establishing a regular review process is vital. It helps ensure that your SOPs stay relevant and effective in this ever-changing industry landscape. By fostering a culture of continuous improvement, your organization can adapt to changes while enhancing productivity and compliance. In a world where operational excellence is everything, committing to creating and maintaining effective SOPs can truly set you apart, driving success and sustainability in manufacturing. So, why not dive in and explore how you can make your SOPs work for you?
Frequently Asked Questions
What is a manufacturing standard operating procedure (SOP)?
A manufacturing SOP is a crucial document that outlines the specific steps needed to carry out tasks consistently and efficiently, ensuring that everyone is aligned to maintain quality standards and comply with industry regulations.
What is the main goal of an SOP?
The main goal of an SOP is to ensure consistency in operations, maintain quality standards, and support ongoing improvement in quality across the organization.
How do SOPs benefit organizations?
SOPs help reduce variability, enhance safety measures, boost overall productivity, streamline workflows, decrease decision-making delays, and lead to cost savings while improving operational efficiency.
What does the Forrester study commissioned by Adobe reveal about digital document procedures?
The study found that 97% of companies had limited or no digital document procedures, highlighting the urgent need for effective manufacturing SOPs in the current landscape.
How can effective SOPs impact operational efficiency?
Well-defined procedures can lead to lower costs, time savings, and increased productivity, as illustrated in case studies like 'Established Procedures Enhance Operational Efficiency.'
What is the first step in creating effective SOP documentation?
The first step is to understand the purpose of SOPs, which will help in developing documentation that aligns with the organization's goals and supports team performance.
How should one define the scope of an SOP?
To define the scope, identify the specific procedures the SOP will cover, consider the tasks needing standardization, and state the objectives such as boosting efficiency, ensuring compliance, or enhancing safety.
Why is it important to monitor changes over time in SOPs?
Monitoring changes and documenting previous versions and reasons for revisions ensures clarity and adaptability, which are essential for maintaining effective SOPs.
What best practices should be followed when setting objectives for SOPs?
Best practices emphasize establishing measurable goals that can evolve with the organization, ensuring that the SOP remains relevant and effective in a fast-paced business environment.
👍
What others are liking
5 Steps to outline your ideal documentation structure
5 MINS READ
Where to start the your journey of mapping out your ideal documentation structure, aligning it with the very heartbeat of your organization?
Defining a winning level of detail in your process
3 MINS READ
What is too much detail, and what is too little? This article described in that winning level detail about what detail is enough.