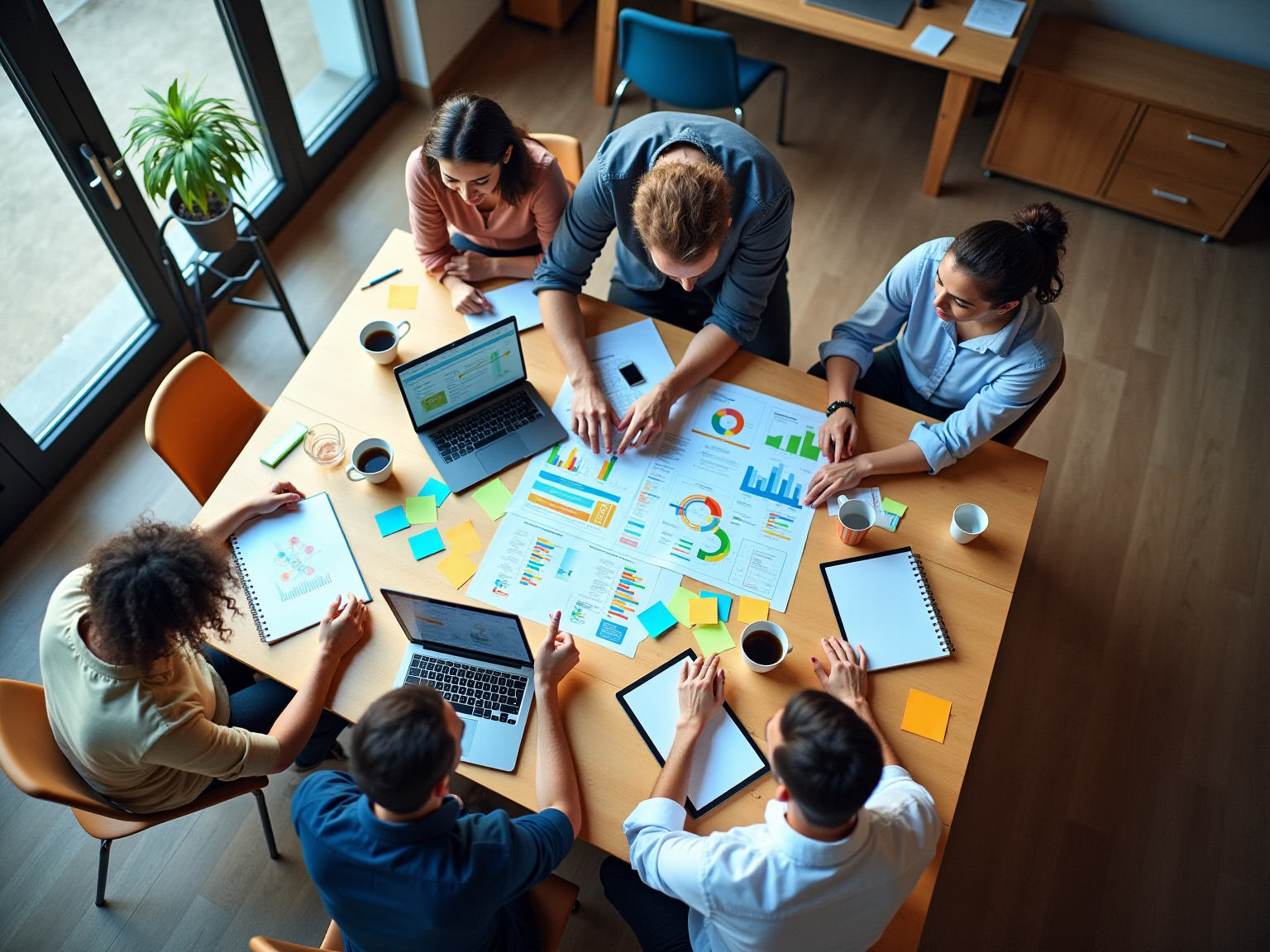
Remote Team Documentation Strategies
|
July 15, 2025
|
10 Working Instructions Examples for Streamlined Operations
Overview
You might be wondering how to make your organization run smoother, right? Well, this article dives into some great examples of working instructions that can really boost operational efficiency in various processes. It’s all about having clear, structured documentation—think Standard Operating Procedures (SOPs), visual instructions, and onboarding guidelines. These tools are essential for cutting down on errors, enhancing training, and making sure everyone’s on the same page when it comes to safety and quality standards. So, let’s explore how these practices can streamline operations in different settings and help you tackle those documentation challenges!
Key Highlights:
- SowFlow enables instant creation of Standard Operating Procedures (SOPs), enhancing operational efficiency and ensuring team access to updated information.
- 97% of organizations lack effective digital document workflows, presenting an opportunity for improved operational consistency.
- Visualized work instructions can reduce errors by up to 80%, improving comprehension and compliance with operational standards.
- Standard Operation Sheets (SOS) provide detailed guidance, boosting product quality and aiding employee training.
- Lockout/Tagout (LOTO) procedures are essential for workplace safety, with comprehensive documentation reducing risk of accidents.
- Gemba walks allow leaders to engage with employees directly, improving process efficiency and fostering teamwork.
- Disaster recovery guidelines are crucial for organizational resilience, with 81% of companies enhancing their strategies post-pandemic.
- ISO 9001 compliance requires clear procedural guidelines to maintain quality standards and improve operational performance.
- Effective onboarding instructions can significantly enhance new employee engagement and retention.
- Clear packaging guidelines can reduce shipping errors by up to 30%, improving logistics efficiency and customer satisfaction.
Introduction
In a world where operational efficiency is key, you might be wondering how businesses are tackling complex processes to boost productivity. Well, innovative solutions are popping up everywhere! Just think about how SowFlow makes creating Standard Operating Procedures (SOPs) a breeze, or how IKEA’s user-friendly assembly instructions have transformed the way we put things together.
As industries change, the value of clear work instructions, Standard Operation Sheets (SOS), and organized onboarding processes really stands out. These tools not only help with compliance and safety but also create a culture of continuous improvement and keep employees engaged.
With advanced technologies on the rise and a stronger focus on quality management, the way we approach operational documentation is evolving. This shift opens up exciting opportunities for organizations to streamline their practices and achieve success.
So, let’s dive into some essential documentation strategies that can enhance efficiency, safety, and overall performance across various sectors!
SowFlow: Instant SOP Creation for Efficient Operations
You might be wondering how to boost your business's operational efficiency, right? Well, SowFlow has got a transformative solution for you! With instant Standard Operating Procedure (SOP) creation, this tool serves as a working instructions example, making it super easy to whip up detailed SOPs in no time. Imagine all your team members having access to the latest and greatest materials—no more outdated info! This not only saves you precious time but also cuts down on the chaos that comes from ineffective documentation practices.
Speaking of chaos, did you know that a Forrester report commissioned by Adobe found that a staggering 97% of organizations have limited or no digital document workflows? That’s a big opportunity for improvement in operational consistency and efficiency! With SowFlow, you can focus on what really matters—your core functions—while keeping your operations structured and uniform.
Now, let’s talk about the benefits of using record-keeping tools. They really streamline processes, enhance knowledge management, and make onboarding new hires a breeze. As the Standard Operating Procedure Management market evolves, it’s crucial for organizations to consider their specific needs, such as a working instructions example. Consider factors like scalability, ease of use, support and training, and pricing when choosing an SOP management solution.
SowFlow is leading the charge in this shift, helping businesses create instant SOPs that drive efficiency and clarity across teams. And here’s something to ponder: a case study on family-operated dairy farms revealed that only 31.3% of these farms utilized written SOPs. This highlights the pressing need for effective documentation solutions like SowFlow to boost operational consistency. So, why not explore how SowFlow can help you enhance your documentation practices?
IKEA: User-Friendly Assembly Instructions for Streamlined Processes
You might be wondering how IKEA has managed to make furniture assembly so much easier for everyone. Well, they’ve really set a standard with their user-friendly assembly guidelines, which serve as a working instructions example designed to simplify the whole process. With clear diagrams and step-by-step instructions, you can navigate through the assembly without feeling lost. This focus on clarity and accessibility serves as a working instructions example that not only boosts customer satisfaction but also helps cut down on those pesky mistakes during assembly. Research even shows that having an effective working instructions example can significantly lower error rates, leading to a better overall experience for customers. Plus, there’s a neat connection between how much assembly work consumers do and how they perceive the value of their purchases, which really underscores the importance of having a working instructions example. This case study shows how proactive guidance can transform the assembly experience. By using computing devices and sensors to track what users are doing, it offers real-time suggestions for the next steps. The results? Not only did it make assembly smoother, but it also reinforced the value customers feel they get from their purchases.
As we look ahead to 2025, IKEA is continuing to innovate its assembly instructions with a strong focus on user-friendly design principles that prioritize your needs. They’re rolling out improved digital interfaces to help you tackle those tricky assembly tasks, and even adding augmented reality features so you can visualize the process. By offering a working instructions example that simplifies assembly through clear guidance, IKEA is not just boosting customer satisfaction; they’re also setting a benchmark for other businesses aiming to enhance their instructional materials. The positive link between well-crafted assembly guidelines and customer satisfaction really highlights why investing in user-friendly documentation is so crucial for any organization looking to improve their operations.
Visualized Work Instructions: Enhancing Clarity and Compliance
You might be wondering how visualized work instructions can really make a difference. Well, they use images, diagrams, and videos to simplify complex information, making everything more accessible and easier to grasp. This approach not only boosts comprehension but also plays a key role in ensuring compliance with safety and operational standards. By integrating these visual elements, organizations can cut down training time significantly—evidence shows that using visuals can lead to an impressive 80% decrease in errors when explaining tasks. Plus, employees feel more prepared to tackle their responsibilities accurately, which is super important in precision-driven industries.
Now, let’s talk about SowFlow's solution. With it, teams can easily create and update user guides, making sure that documentation stays relevant and accessible. Speaking of that, a cross-industry study by PwC in 2022 found that teams using advanced visualization dashboards made critical production decisions 32% faster than those sticking with traditional reporting methods. That really highlights the competitive edge you can gain through effective visual communication.
Looking ahead, Gartner’s Manufacturing Technology Trends (2023) predicts that by 2025, over 75% of large manufacturers will have implemented at least one of these advanced visualization approaches. This reflects a shift toward more efficient and compliant operational practices. As we approach 2025, the trend of adopting visualized working instructions examples is expected to grow, highlighting the importance of visual aids in enhancing operational efficiency. So, are you ready to explore how these tools can transform your documentation process?
Standard Operation Sheets: Ensuring Consistency in Manufacturing
You might be wondering why Standard Operation Sheets (SOS) are such a big deal in manufacturing. Well, these handy resources serve as a working instructions example, providing detailed guidance for specific procedures to ensure everything runs smoothly and consistently. By using a working instructions example to document the best methods and practices, organizations can really cut down on variability, which in turn boosts product quality. In fact, companies that embrace SOS often notice a significant uptick in efficiency and a drop in production errors.
But that’s not all! SOS also play a crucial role in training new employees by offering a working instructions example. Think of them as reliable references for best practices that can speed up onboarding and foster a culture of continuous learning. Did you know that employees with access to ongoing training resources are 47% more likely to feel engaged at work? That’s a compelling reason to prioritize comprehensive learning options, and SOS can definitely help by providing a working instructions example along with clear, accessible documentation that enhances training effectiveness.
Now, let’s talk about the importance of consistency in production processes. Expert opinions highlight that it’s essential for maintaining high standards and achieving operational excellence. Ralph Waldo Emerson once said, "Do not go where the path may lead, go instead where there is no path and leave a trail." This idea fits perfectly with how SOS can be innovatively applied in manufacturing, encouraging companies to carve their own paths toward efficiency.
Looking ahead to 2025, the role of SOS in manufacturing is only going to grow. More and more companies are recognizing how these sheets act as a working instructions example to help standardize procedures and enhance training effectiveness. Case studies show that organizations using SOS experience smoother transitions for new hires, thanks to the clear guidance that reduces errors and miscommunication. In larger companies, the Learning and Development (L&D) team usually oversees training, while in smaller firms, current team members often step up to take on that role. By making SOS a priority, manufacturers can ensure that every team member is on the same page with best practices, leading to a more efficient and productive work environment. So, if you’re an operations manager, consider weaving SOS into your training programs and keep them updated to reflect the latest best practices and process improvements. Let’s make the most of these valuable tools!
Lockout/Tagout Procedures: Safety Instructions for Operational Compliance
Lockout/Tagout (LOTO) procedures are super important safety protocols that protect you and your coworkers from hazardous energy while maintaining and servicing machinery. You might be wondering, what exactly do these procedures involve? Well, they outline specific steps for isolating energy sources, ensuring that equipment can't accidentally spring to life. Keeping effective LOTO records is crucial for staying compliant with safety regulations and helps build a safety-first culture in your organization. Did you know that improper equipment lockout is linked to up to 10% of industrial safety incidents? That really highlights the need for clear and accessible LOTO instructions to significantly reduce the risk of workplace accidents.
Now, let’s talk about how SowFlow can make your life easier. It empowers operations managers by providing an intuitive platform for creating user guides, so your team can whip up thorough LOTO records without breaking a sweat. With features like instant updates and easy access to resources, you can ensure that your LOTO procedures are always up-to-date and right at your fingertips. This not only boosts productivity but also reinforces the importance of sticking to effective safety protocols.
But wait, there’s more! The financial fallout from not following LOTO regulations can be pretty harsh. Non-compliance can lead to hefty penalties, and OSHA data shows that repeated violations can result in major fines. For example, the case study titled 'Financial Impact of LOTO Violations' shows how businesses can face serious financial consequences for not keeping up with these regulations. It really drives home the point that companies need to prioritize effective LOTO record-keeping, as it directly impacts workplace safety and compliance. Plus, LOTO regulations are getting stricter, so navigating these changes is essential to keep your operations compliant and prevent avoidable injuries and fatalities.
Incorporating expert insights into the importance of LOTO procedures really emphasizes how critical they are. The National Safety Council points out that a worker is injured every seven seconds, which underscores the urgent need for strong safety measures. By ensuring that your LOTO records are comprehensive and up-to-date with SowFlow's solution, you can enhance operational compliance and protect your workforce from potential hazards. So, operations managers, make it a priority to keep LOTO records as a key part of workplace safety. You want to ensure that all procedures, including a working instructions example, are clearly outlined and easy to access. To really maximize safety and compliance, why not consider implementing SowFlow for your LOTO documentation needs?
Gemba Walks: Structured Instructions for Process Improvement
Have you ever thought about how important it is for leaders to get out there and see the work being done? Gemba walks are all about visiting the 'real place' where the action happens. This hands-on approach allows leaders to observe processes and engage directly with employees, which is crucial for spotting inefficiencies and gathering those golden insights from the workforce. By following a working instructions example during Gemba walks, leaders can significantly enhance their effectiveness, ensuring they ask the right questions and focus on the key areas that need improvement. When there's open dialogue and teamwork, Gemba walks can lead to some impressive enhancements in operational processes.
Now, let’s talk about SowFlow's immediate documentation solution. It makes creating user guides a breeze, providing a working instructions example that simplifies the process of developing structured instructions for Gemba walks. This not only helps standardize procedures but also makes onboarding and knowledge sharing a whole lot easier, ultimately ramping up team efficiency. Research shows that organizations that adopt structured Gemba walks see some serious gains—think cycle times cut by up to 20% and defect rates dropping as much as 15%. That’s a big deal for overall productivity! For example, a recent case study highlighted how a structured approach to Gemba walks helped a product team streamline their onboarding process, slashing training time by 30%. This structured method not only boosts leadership engagement but also empowers teams to tackle unexpected issues. It really drives home the importance of keeping an open mindset during these observations, as Jan Hebborn emphasizes.
Speaking of communication, it’s key during Gemba walks. Talita Guerra Frinzi points out that effective communication is essential for showcasing improvements and ensuring everyone is on the same page with operational goals. To wrap it all up, incorporating organized working instructions examples into Gemba walks, supported by SowFlow's record-keeping features, not only enhances their efficiency but also fosters a culture of continuous improvement. So, to really maximize the benefits of Gemba walks, why not make it a habit to regularly update your documentation with SowFlow? Keeping it fresh and aligned with your operational goals can make a world of difference!
Disaster Recovery Instructions: Ensuring Operational Resilience
Disaster recovery guidelines are all about the essential actions you need to take to get things back on track after something disruptive happens—think natural disasters or cyberattacks. It’s super important that these guidelines are clear, detailed, and easy to find, so everyone knows what their role is when it’s time to recover. A well-documented disaster recovery strategy not only cuts down on downtime but also protects those crucial assets, boosting your company’s resilience against unexpected challenges.
You might be wondering how to keep these guidelines fresh and relevant. That’s where SowFlow comes in! With SowFlow, creating and updating your disaster recovery guidelines becomes a breeze. Just a single command lets you tap into your records, giving your team immediate access to vital information. This means fewer unnecessary meetings and much better communication when emergencies strike. To really make the most of SowFlow for your disaster recovery planning, start by outlining the key recovery processes and creating a working instructions example for your team members. Then, use SowFlow to craft a structured template for these working instructions examples, incorporating relevant screenshots to make everything crystal clear. Don’t forget to keep those records updated to reflect any changes in processes or staff, so everyone can access the latest info.
The importance of disaster recovery planning has really come to light lately. Did you know that 81% of organizations have improved their business continuity strategies in response to the pandemic? It’s clear that having solid disaster recovery guidelines is key to making it all work. Plus, a whopping 87% have shown a renewed commitment to this planning, highlighting the growing recognition of the need for organized records. This proactive approach is especially crucial when you consider the staggering 144% increase in the average ransom demanded during cyber incidents reported in 2022. According to the Palo Alto 2022 Unit 42 ransomware threat report, businesses faced an 85% rise in incidents where employees' personal data was compromised, underscoring the urgency for robust disaster recovery plans.
Now, let’s talk about best practices! Regularly testing your disaster recovery plans is essential to ensure they’re effective and relevant. Organizations should aim to conduct these tests at least once a year to prepare staff for real-life scenarios, reinforcing operational resilience. In fact, 97% of data is reportedly recoverable after a ransomware attack, which really emphasizes the importance of having clear recovery guidelines in place to make that happen. Ultimately, the impact of well-defined disaster recovery protocols on operational resilience is huge. They not only help you bounce back quickly but also instill confidence among employees, ensuring everyone is aligned and ready to respond effectively to crises. With SowFlow’s solution, companies can revolutionize their documentation methods, boosting productivity and making sure disaster recovery plans are always current and accessible.
ISO 9001 Compliance: Work Instructions for Quality Management
You might be wondering how ISO 9001 compliance works. Well, it requires organizations to create clear procedural guidelines, such as a working instructions example, that outline exactly how tasks should be done to meet quality standards. These guidelines are super important for keeping everything consistent across operations and making sure all team members are on the same page with the quality management practices. By sticking to ISO 9001 guidelines, businesses can really ramp up their operational efficiency and boost customer satisfaction by delivering reliable, high-quality products and services.
Now, let’s dive into some recent research. It suggests that companies should see ISO standards as part of a long-term continuous improvement strategy. This approach not only enhances operations but also leads to better overall performance. Just look at organizations that prioritize a working instructions example; their commitment to quality management shines through in their operational success, creating a more organized and efficient workplace.
As Dr. Adalia Martin, Head of Quality Assurance Centre, puts it, "Organizational commitment was strongly related to both operational performance and business performance." So, how can you enhance your quality management practices? Consider leveraging technology like SowFlow. Product Owner Anastasia Masadi describes it as a game changer for documenting work and delivering to clients. She shares, "I do not have to take each screenshot separately, and do not even have to leave the browser while I am creating SOPs and training materials. SowFlow gave me time from my life back." This really highlights how SowFlow helps teams create SOPs and training resources on the spot, ensuring consistency in work guidelines while revolutionizing record-keeping.
Also, while ISO 45001 certification is all about occupational health and safety, it emphasizes the importance of corporate responsibility in quality management. For operations managers, a working instructions example is essential for having comprehensive work guidelines. Make sure your team reviews and updates these documents regularly to maintain compliance and operational excellence. Why not book a demo today to see how SowFlow can transform your documentation processes?
Onboarding Instructions: Streamlining New Employee Training
Induction guidelines are super important for helping new staff get the hang of their roles and the company vibe. You might be wondering what these guidelines should include. Well, they should cover:
- Company policies
- Job responsibilities
- Key resources
to make sure the transition is smooth. By simplifying the onboarding process with a working instructions example that is clear and comprehensive, companies can really boost employee engagement and retention. In fact, did you know that 65% of HR professionals think that using artificial intelligence in onboarding will positively impact employee retention rates?
Now, let’s talk about SowFlow's instant documentation solution. It empowers organizations to whip up user guides effortlessly, ensuring that onboarding materials are always fresh and relevant. This not only makes standardization easier but also enhances knowledge sharing among teams, which ultimately cranks up productivity. Looking ahead to 2025, best practices for onboarding highlight the need for clarity and accessibility in training materials. Have you ever thought about using innovative methods like virtual reality (VR)? They can create immersive experiences that help new hires feel more confident and less stressed. For example, VR can offer virtual office tours and realistic job simulations, making onboarding way more engaging and effective. A case study titled "Virtual Reality in Onboarding" shows how VR can enhance the onboarding experience by providing immersive opportunities, helping new hires adapt to their roles with ease.
Furthermore, a working instructions example is essential for new staff as part of transparent onboarding procedures since they directly affect retention. Organizations that implement a working instructions example as part of their structured onboarding are likely to see new hires becoming more productive, as they spend less time figuring things out and more time contributing to their teams. By embracing SowFlow's efficient onboarding guidelines, companies can build a more productive workforce and lay the groundwork for long-term employee success. And remember, the time spent on onboarding will vary depending on the job role, so it’s crucial to keep the process adaptable and effective for everyone.
Packaging Instructions: Ensuring Efficiency in Logistics
You might be wondering how packaging guidelines can make a difference when it comes to shipping products. Well, they lay out the essential steps for preparing items for transit, covering everything from materials to handling procedures and labeling requirements. Having clear and comprehensive packaging guidelines is super important for cutting down on errors and minimizing damage during shipping. This not only boosts logistics efficiency but also keeps customers happy.
For instance, companies that implement straightforward packaging guidelines can significantly reduce shipping mistakes, which in turn enhances operational efficiency and increases customer satisfaction. Did you know that efficient packaging methods can cut shipping errors by as much as 30%? That really highlights how crucial precision is in these guidelines. Plus, a recent study found that 72% of American consumers consider packaging design to be a key factor in their purchasing decisions. This just goes to show how vital it is for businesses to focus on quality and sustainability in their packaging.
Now, let’s dive into how logistics technology is evolving. As it advances, effectively managed packing lists are becoming more critical than ever. The 3D-printed packaging market is expected to reach a whopping $1,210 million in 2023, showcasing a shift towards innovative solutions that enhance logistics efficiency.
Speaking of shifts, consumer preferences are changing too! Sustainable products are growing 2.7 times faster than traditional options, emphasizing the importance of sustainability in packaging. Europe is leading the way with its sustainable packaging regulations, and businesses in North America and the Asia-Pacific are starting to adapt to similar changes. This reflects a growing desire among consumers for environmentally friendly packaging. By adopting a working instructions example in packaging instructions, organizations can not only improve logistics efficiency but also meet the evolving expectations of consumers and regulatory standards.
Conclusion
You might be wondering how effective documentation strategies can really make a difference. Well, it turns out that they’re absolutely essential for boosting efficiency, safety, and overall performance across various industries. Just look at SowFlow's innovative approach to crafting Standard Operating Procedures or IKEA's user-friendly assembly instructions—clarity and accessibility are key! These tools not only streamline processes but also help cultivate a culture of continuous improvement and keep employees engaged.
Have you ever thought about how visualized work instructions and Standard Operation Sheets can cut down on mistakes? They can also make training way more effective, leading to a more productive workforce. Plus, integrating Lockout/Tagout procedures and disaster recovery instructions highlights just how important safety and resilience are in operational compliance. As organizations navigate ever-evolving challenges, having structured documentation is crucial for maintaining quality management and aligning with industry standards like ISO 9001.
As industries keep pushing the envelope, adopting comprehensive onboarding instructions and packaging guidelines becomes vital for enhancing logistics efficiency and meeting customer expectations. The future of operational documentation looks bright, especially with tools like SowFlow enabling organizations to adapt and thrive in today’s dynamic business landscape.
So, let’s wrap this up! Prioritizing effective documentation strategies isn’t just about ticking boxes for compliance; it’s truly a pathway to operational excellence. By investing in clear, accessible, and user-friendly documentation, organizations can tackle complexities with ease, boost productivity, and ultimately achieve lasting success in their fields. How exciting is that?
Frequently Asked Questions
What is SowFlow and how does it improve operational efficiency?
SowFlow is a tool that enables instant creation of Standard Operating Procedures (SOPs), providing easy access to up-to-date working instructions. This helps streamline operations, saves time, and reduces chaos caused by ineffective documentation practices.
What is the significance of the Forrester report mentioned in relation to digital document workflows?
The Forrester report commissioned by Adobe found that 97% of organizations have limited or no digital document workflows, indicating a significant opportunity for improvement in operational consistency and efficiency.
How do record-keeping tools benefit organizations?
Record-keeping tools streamline processes, enhance knowledge management, and simplify the onboarding of new hires, making them essential for effective operational practices.
What factors should organizations consider when choosing an SOP management solution?
Organizations should consider scalability, ease of use, support and training, and pricing when selecting an SOP management solution.
What does the case study on family-operated dairy farms reveal about SOP usage?
The case study revealed that only 31.3% of family-operated dairy farms utilized written SOPs, highlighting the need for effective documentation solutions like SowFlow to improve operational consistency.
How does IKEA simplify furniture assembly for customers?
IKEA uses user-friendly assembly guidelines that include clear diagrams and step-by-step instructions, which simplify the assembly process and enhance customer satisfaction by reducing mistakes.
What innovations is IKEA implementing for its assembly instructions?
IKEA is rolling out improved digital interfaces and augmented reality features to help customers visualize and tackle assembly tasks more easily.
How do visualized work instructions enhance understanding and compliance?
Visualized work instructions use images, diagrams, and videos to simplify complex information, boosting comprehension and ensuring compliance with safety and operational standards.
What impact do visual aids have on training time and error rates?
Evidence shows that using visual aids can lead to an 80% decrease in errors when explaining tasks, significantly reducing training time and preparing employees to perform their responsibilities accurately.
What is the trend regarding advanced visualization approaches in manufacturing?
According to Gartner’s Manufacturing Technology Trends (2023), over 75% of large manufacturers are expected to implement advanced visualization approaches by 2025, indicating a shift towards more efficient operational practices.
👍
What others are liking
5 Steps to outline your ideal documentation structure
5 MINS READ
Where to start the your journey of mapping out your ideal documentation structure, aligning it with the very heartbeat of your organization?
Defining a winning level of detail in your process
3 MINS READ
What is too much detail, and what is too little? This article described in that winning level detail about what detail is enough.